This order commissioned by a single customer involves the production of two different mixers for semi-dense products with a food application, specifically
– 300-litre heated mixer
– 700-litre cold mixer.
The customer, who already had an old plant, contacted us for advice related to the need to increase existing production volumes by doubling the production of cold products and to introduce new hot mixed products. The proposed plants are suitable for handling liquids and powders in the food industry.
The initial phase involved our team working with the customer’s technicians to refine the project: in particular, about a month after the order was placed, we discussed the designed plant and defined the details to be fixed before going into production.
Specifications made on installations:
Given that the machinery is used in the food industry, we opted for AISI 316 steel for all components in contact with the product, also paying particular attention to the choice of material for the various gaskets and wall scrapers.
The choice of agitators inside the mixing tank was well thought out and defined thanks also to the decision to work directly with the customer during the design phase, so as to be able to define a tailor-made solution for the customer’s flagship product, but also allowing the customer the flexibility to process a wider range of products.
Type of agitators envisaged
On both machines we have installed a weight control system using load cells, which also allows automatic control of the preloading of the liquid product to be mixed.
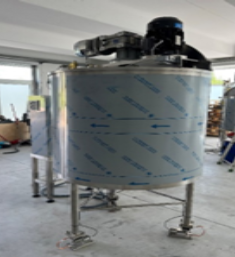
For the hot mixer, a heating water recirculation system has been designed that can be connected to their chiller network. Having a heating circuit and not a simple immersion tank results in a saving of the water used by the customer and increases the thermal efficiency of the cavity so as to maximise the heating time and subsequent cooling of the product inside the mixing tank; everything is controlled by means of a programme that can be set by the operator from the touch screen panel. Since the heating is done using water, which is brought very close to boiling temperature, special attention has been paid to the safety of the system itself; therefore all the components have been included that allow for a performance that is as high performance as it is safe both for the product and above all for the operators and company.
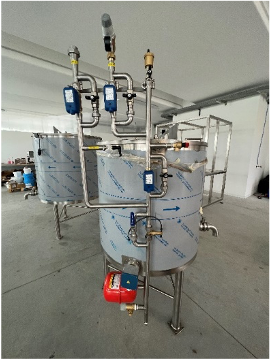
The order was realised in 4 months from the order with a phase of customer shadowing for the first production runs.