This order involved the creation of a line for the packaging for various types of cosmetic products in different formats: the customer, a third-party cosmetic production laboratory, needed a versatile solution adaptable to a variety of containers and caps that are offered to him in turn by their customers.
A monoblock with manual loading of the caps onto the transport belt was proposed, evaluating both the required production speeds (max. 1,000 pcs/h) and the need to produce small batches, thus reducing the format change time which takes place in less than 10 minutes.
The system has been supplied with a software with the predisposition to foresee the addition of further components such as the incoming or outgoing rotary tables, the vibrating cap loading orientator, the additional dosing group without having to foresee the withdrawal of the machine if the need was to increase its performance.
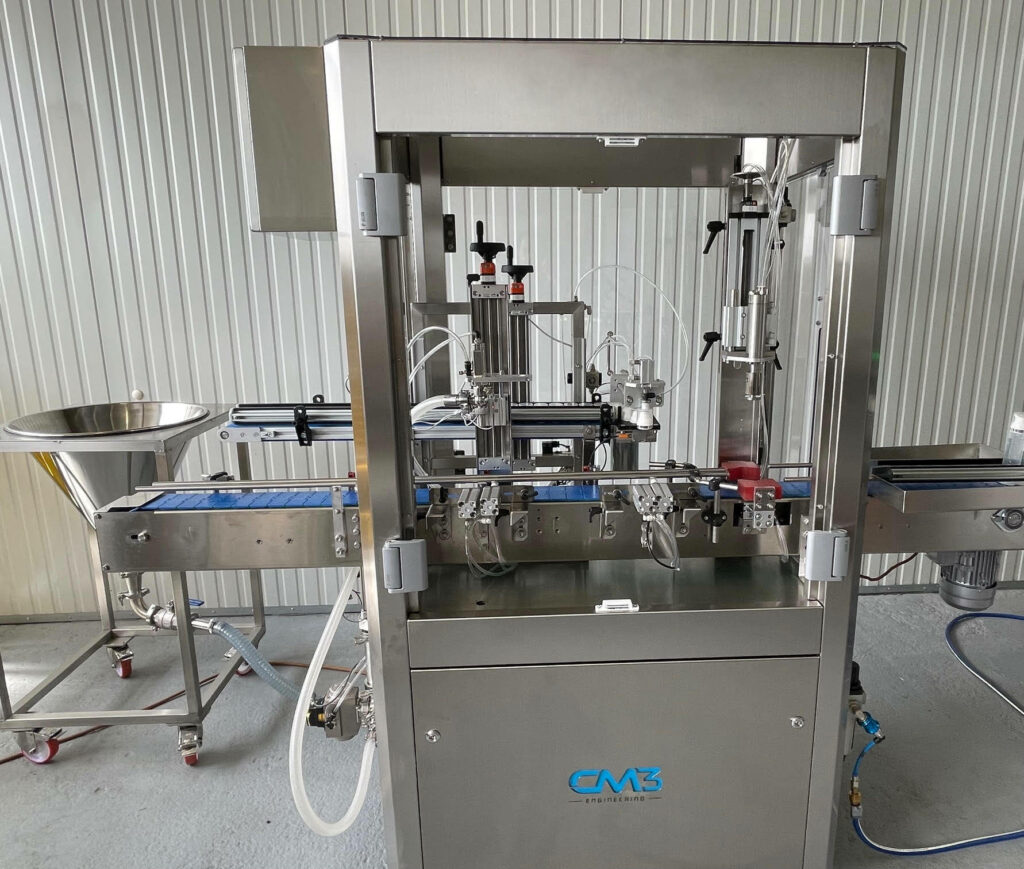
Foto impianto realizzato
The installed volumetric dosing group has a range capable of managing doses from 5 ml up to 250 ml in a single stroke on which it is possible to install different dispensing spouts with various diameters based on the mouth of the bottle. The suction cup pick&place takes the caps from the appropriate belt, placing it in the neck of the filled container. (photo 2)
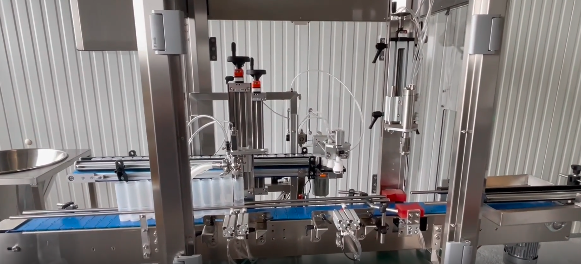
Fot. 2 Dettagli gruppo di dosaggio, pick&place
The process is completed by a pressure capper moved by a pneumatic motor with a special stainless steel insert. (photo 3)
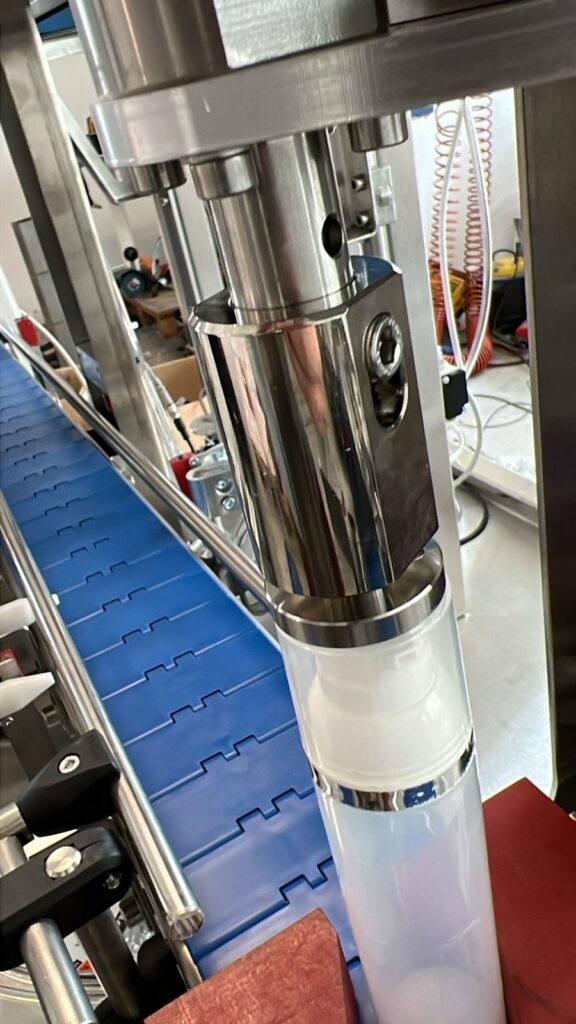
Fot. 3 Tappatore a pressione
The system was also combined with a 30 liter product collection hopper inserted in a special trolley that can be moved on wheels.
The line is able to manage the dosing of liquid and semi-dense (gel-type) products of different viscosities with a production output of approximately 1,000 pcs/h on a 100 ml format.