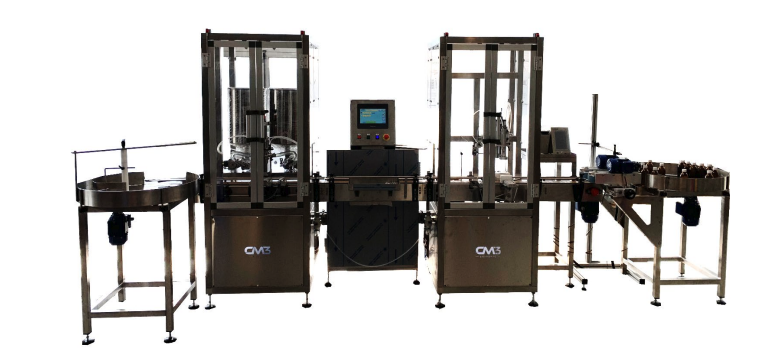
In this order, our team assisted the customer in the start-up of a cosmetic laboratory, supporting them from the beginning in proposing the best solution that would meet three requirements:
1) A versatile line capable of handling a total of 6 formats, from the smallest 20ml metal bottle to the largest 500ml glass bottle with screw cap
2) A modular solution designed for future expansion and automation
3) A solution that was in line with the available budget
The design of the system took into account the space of the customer’s new laboratory from the outset by adapting the line’s dimensions to the floor plan provided and the remaining available space.
The plant, also with a view to future expansion, is equipped with two pneumatically operated volumetric dosers with a dosing range from 5ml to 380ml.
This range allows all formats to be handled in a single stroke and the larger 500ml format in two strokes.
In order to guarantee an adequate supply ‘lung’ during the filling phase, two hoppers of 50 litres each (one for each dispenser) have been provided so that the plant can guarantee the production speeds required now and in the future.
The capping monoblock, on the other hand, has been specially designed with the space required to be able to add a possible pick & place station for automatic cap positioning at a later stage, a scenario that will allow the customer, when production volumes justify it, to free up additional operator time, which will be limited to just managing product loading and unloading at the start and end of the line.
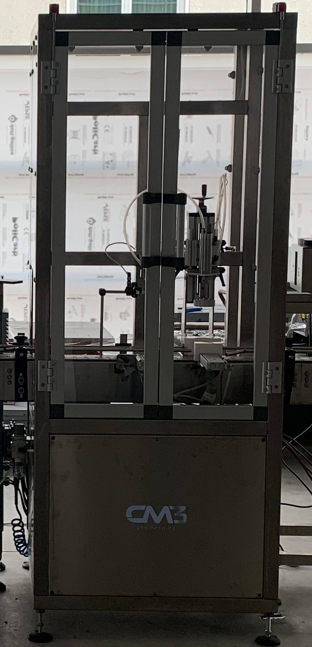
To allow for this future modification, not only the capping unit but also the entire electrical control panel of the machine was specially dimensioned for the necessary automation additions.
The adjustments for the six format changes are simple and easy to learn, and take the form of a few easy manual adjustments of the dosing and capping stations as well as the jar conveyor belt.
The machine can also be operated by a single operator who will load the empty jars onto the inlet rotary table and then position himself at the station in front of the touch screen panel, load the specific processing recipe and start the system. With the machine running, the operator will have to manually place the cap over the jar that will be unloaded into the rotary table at the end of the line.
Production speeds are between 1,000 and 1,200 pcs/h (with a two-operator machine management) numbers that can be increased to 1,800 pcs/h with the addition of the automatic cap loading system. (in this case the presence of the second operator would also be eliminated)
At the end of the line, between the capping station and the rotating unloading table, an ink-jet marker was required to print the expiry date batch, which is placed on a small, purpose-built four-legged frame.

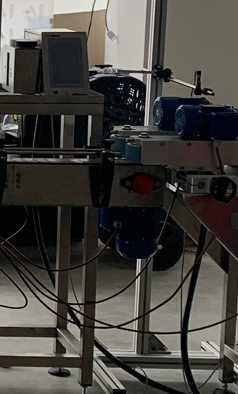
The realisation and delivery of the system took about 4 months from the order and, after an initial test at CM3’s premises, the installation, commissioning and training of the employees lasted a total of 4 days, followed by remote support activities at the customer’s need with the activation of a service contract.
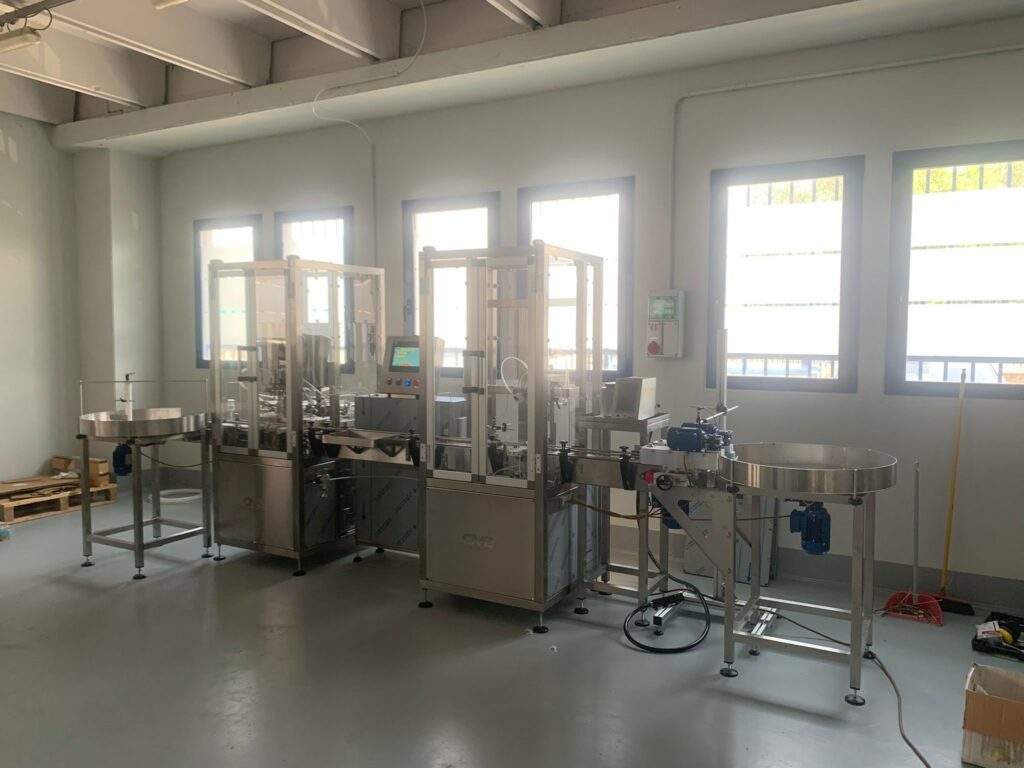
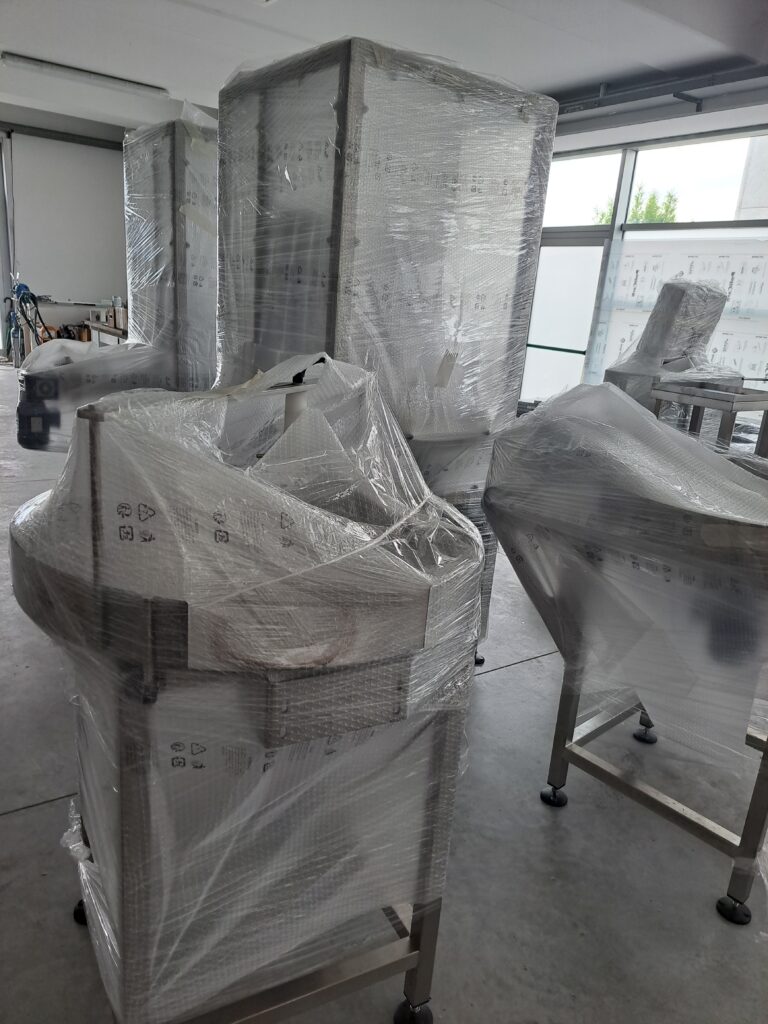
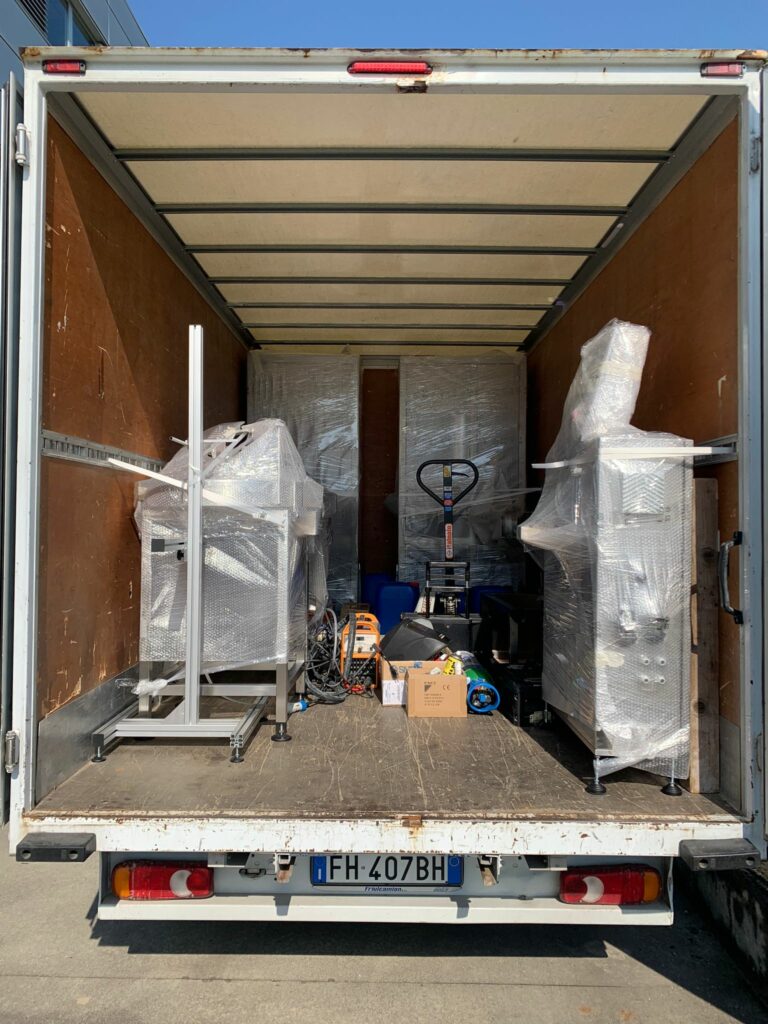