This job involved the study and tailor-made realisation of an automatic line suitable for the packaging process of powdered products inside a cylindrical metal container on which, after the product filling phase, the silicone is applied and the lid tightened through a clinching process.
In order to define the layout of the plant, visible in the photo below, our engineering team was engaged for about three months in the activities of studying, fine-tuning and selecting the appropriate materials to handle the powders and the various stations that are part of the entire packaging process.
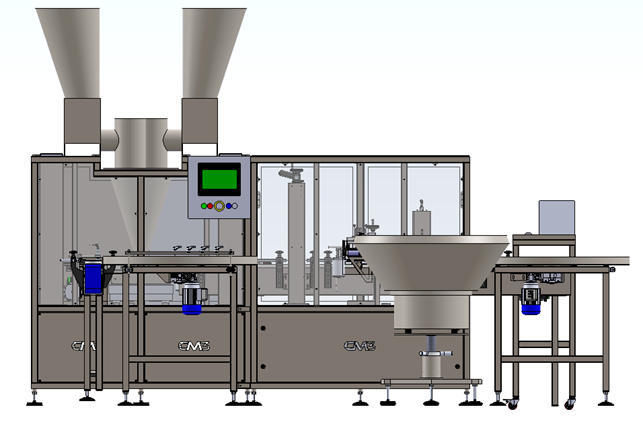
Complete plant layout in 3D
A Ø 1,000 rotary table was provided to allow the empty boxes to be loaded into the packaging line at approximately every hour of processing.
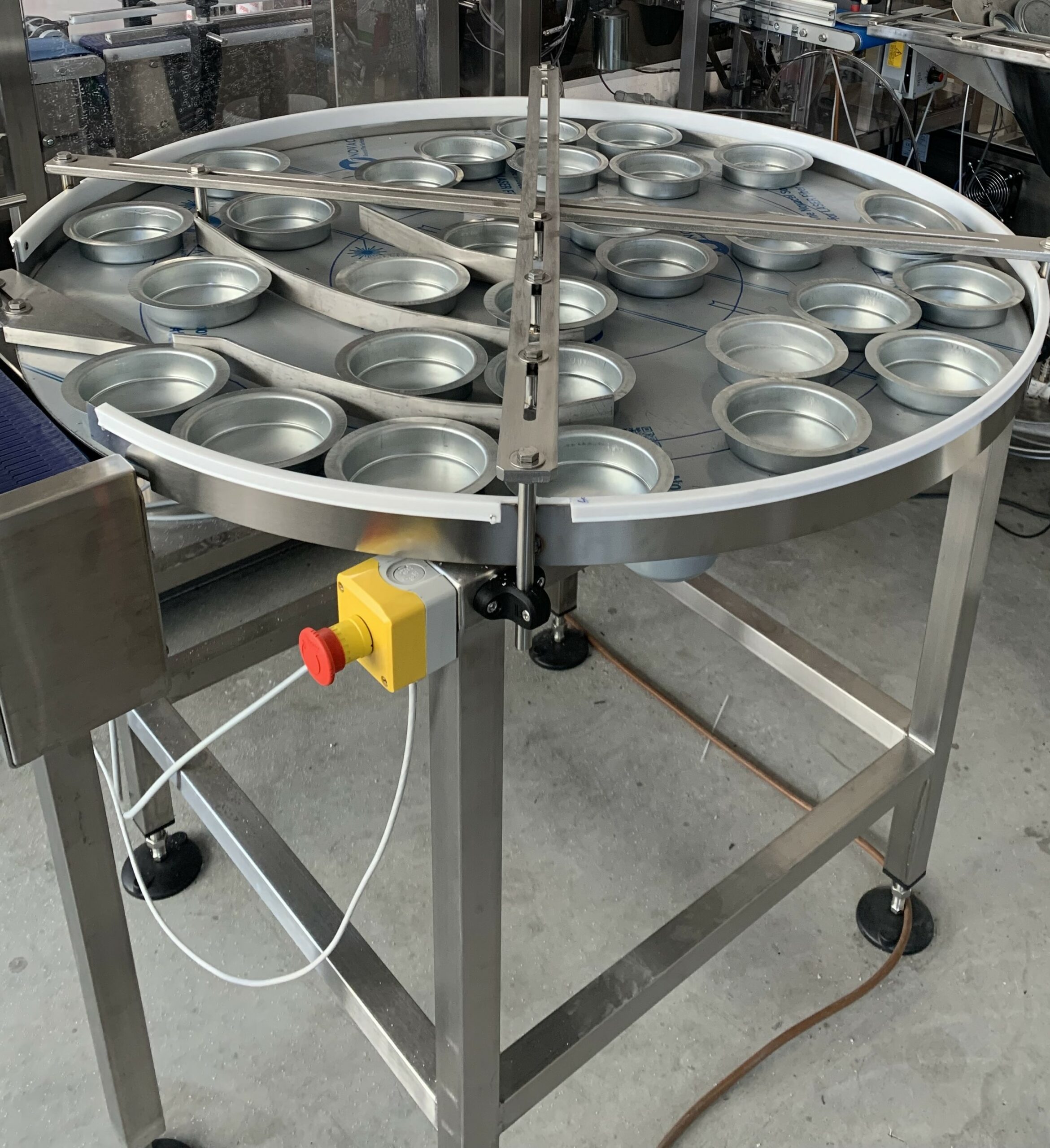
Photo rotating container loading table at the beginning of the line
At the inlet of the monobloc is the dosing station consisting of two separate screw feeders with loading hoppers specially made in stainless steel and lined with expanded hastelloy C-276 PTFE into which two different products are loaded.
The product is conveyed into a conical hopper that drops the product into the container resting on a special load cell that monitors the correct weight. The standard dosing process is carried out through three automatic steps: PRODUCT A (weight) – PRODUCT B (weight) and PRODUCT A (weight). The different processing recipes, individual weights and product rates can be set from the touch screen panel.
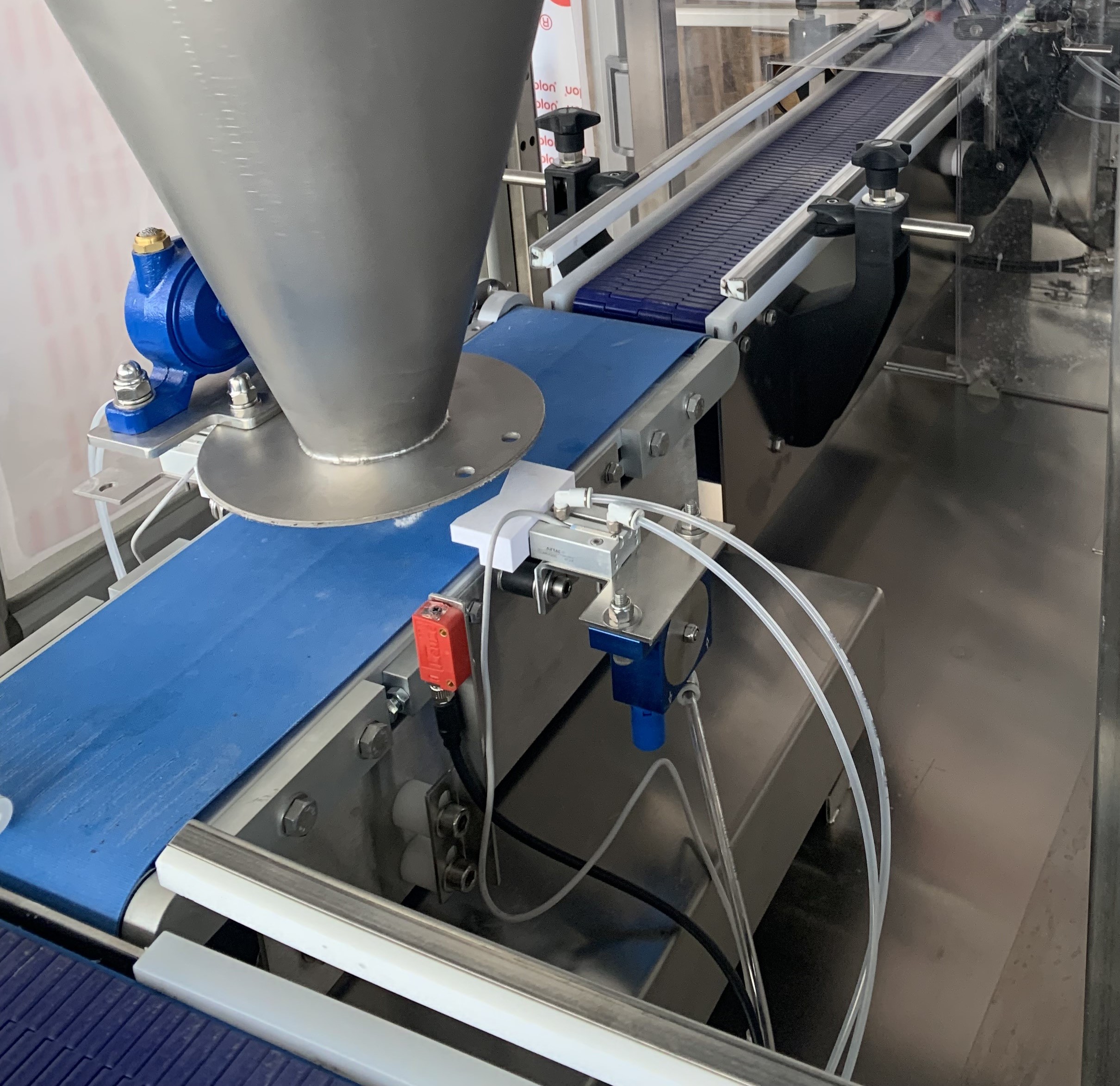
Picture dosing station on load cell
Continuing the processing cycle we find the siliconising station where, by means of rotating modules, the container is rotated to allow the silicone to be dispensed around the entire edge.
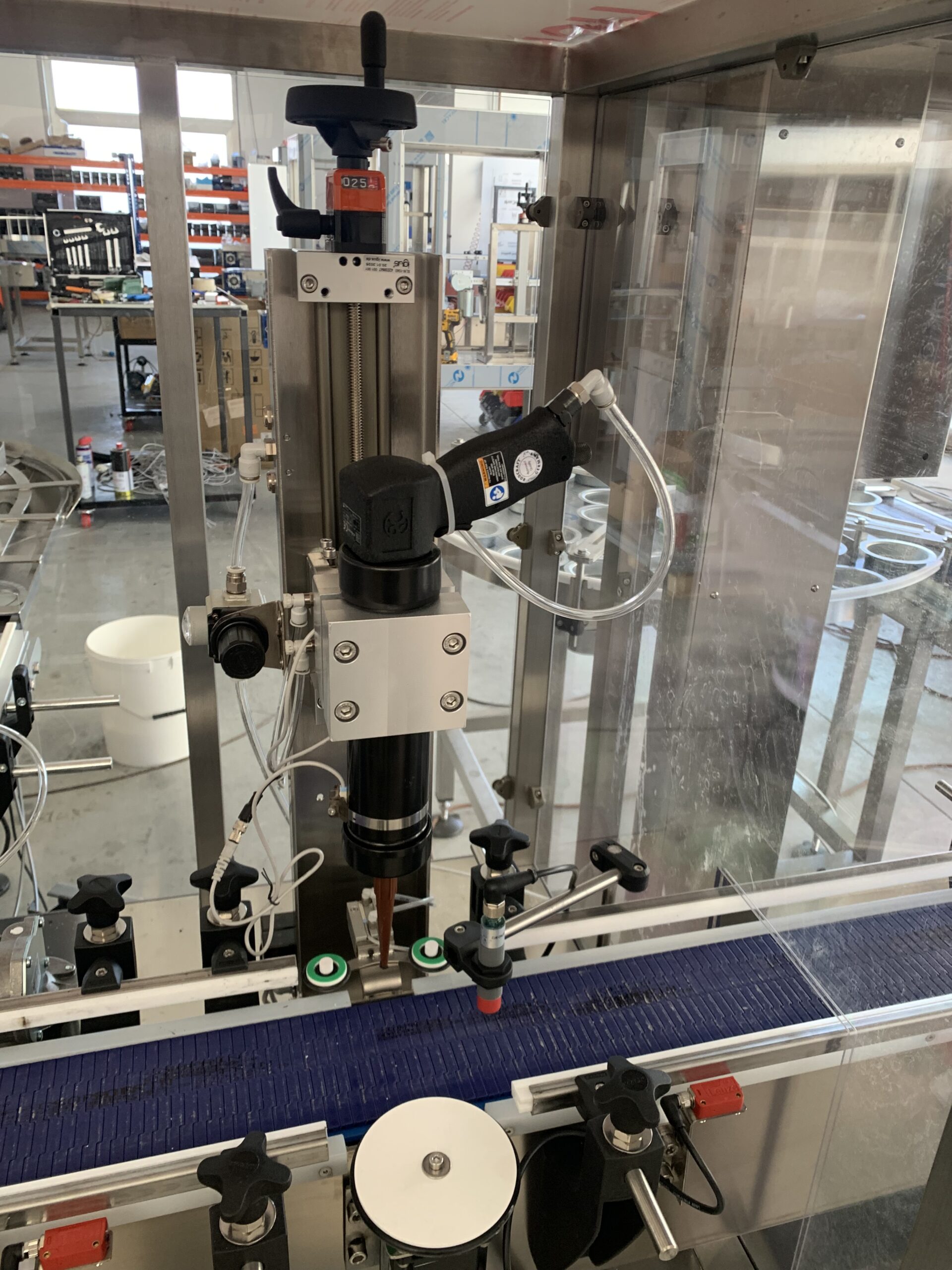
Siliconizing station with rotation system
Next, the pick-and-place picker picks up the lids, which are automatically loaded onto the special belt by a vibrating orientator, and places them on top of the container, applying gentle pressure to allow the silicone to set quickly.
The last packaging stage, clinching, is designed using the same rotation principle by punching the lid onto the container at 7 separate points.
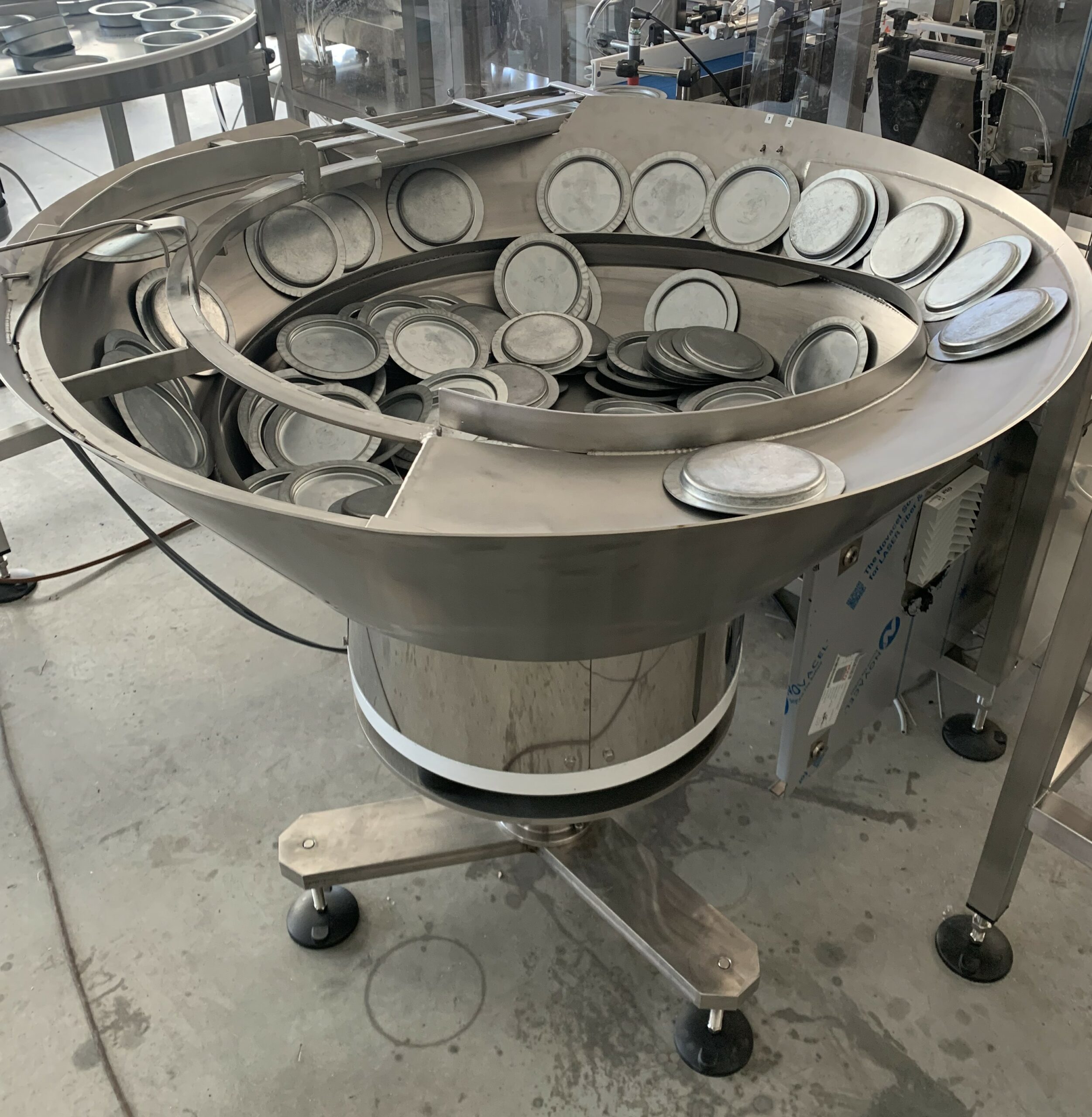
Image Vibrating metal lid orientator
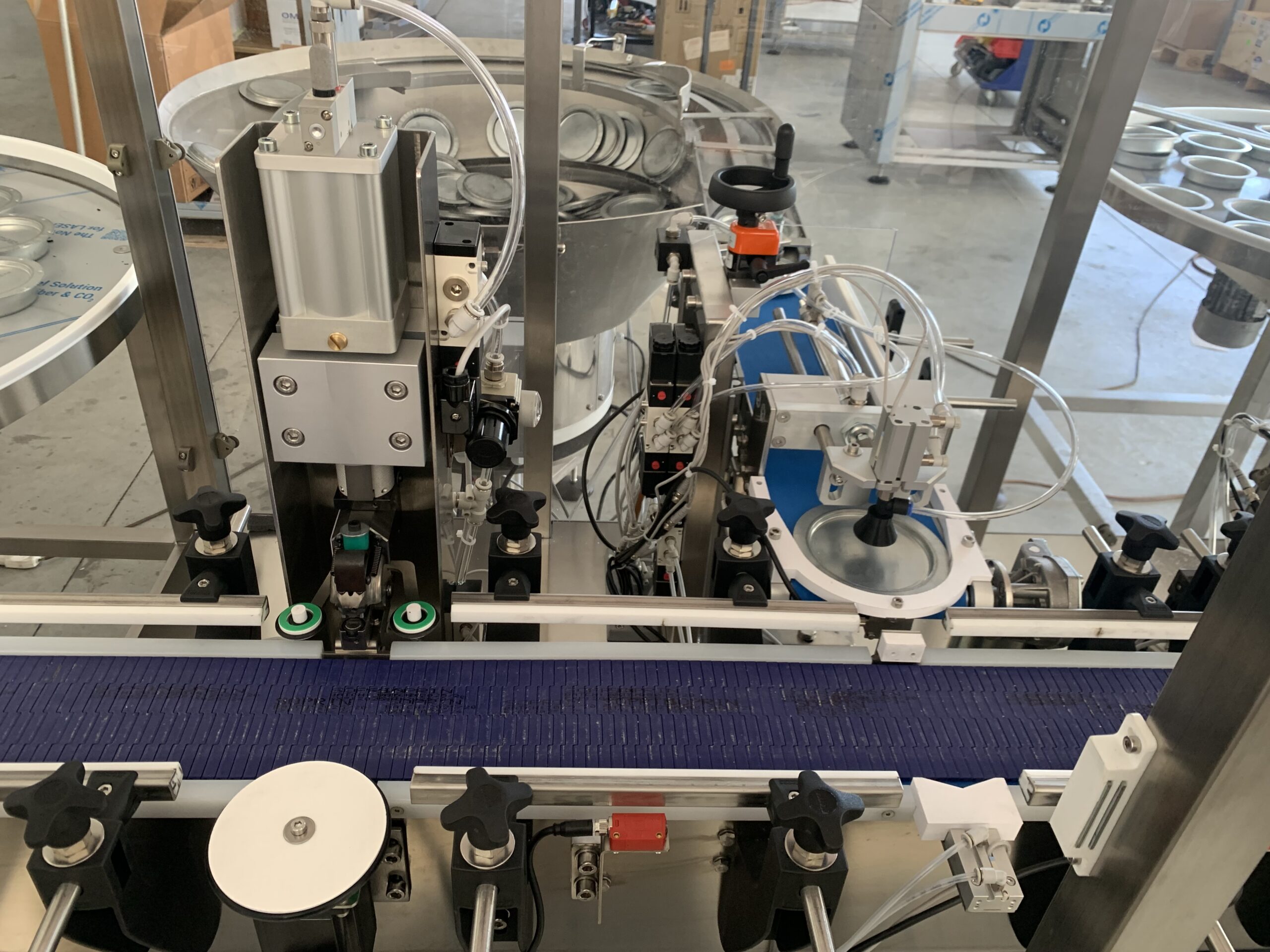
Image of PICK&PLACE pick and place station
Finally, at the outlet of the monoblock we find a thermal transfer marker for printing the production batch and product mark, and a Ø 1,000 accumulation rotary table.
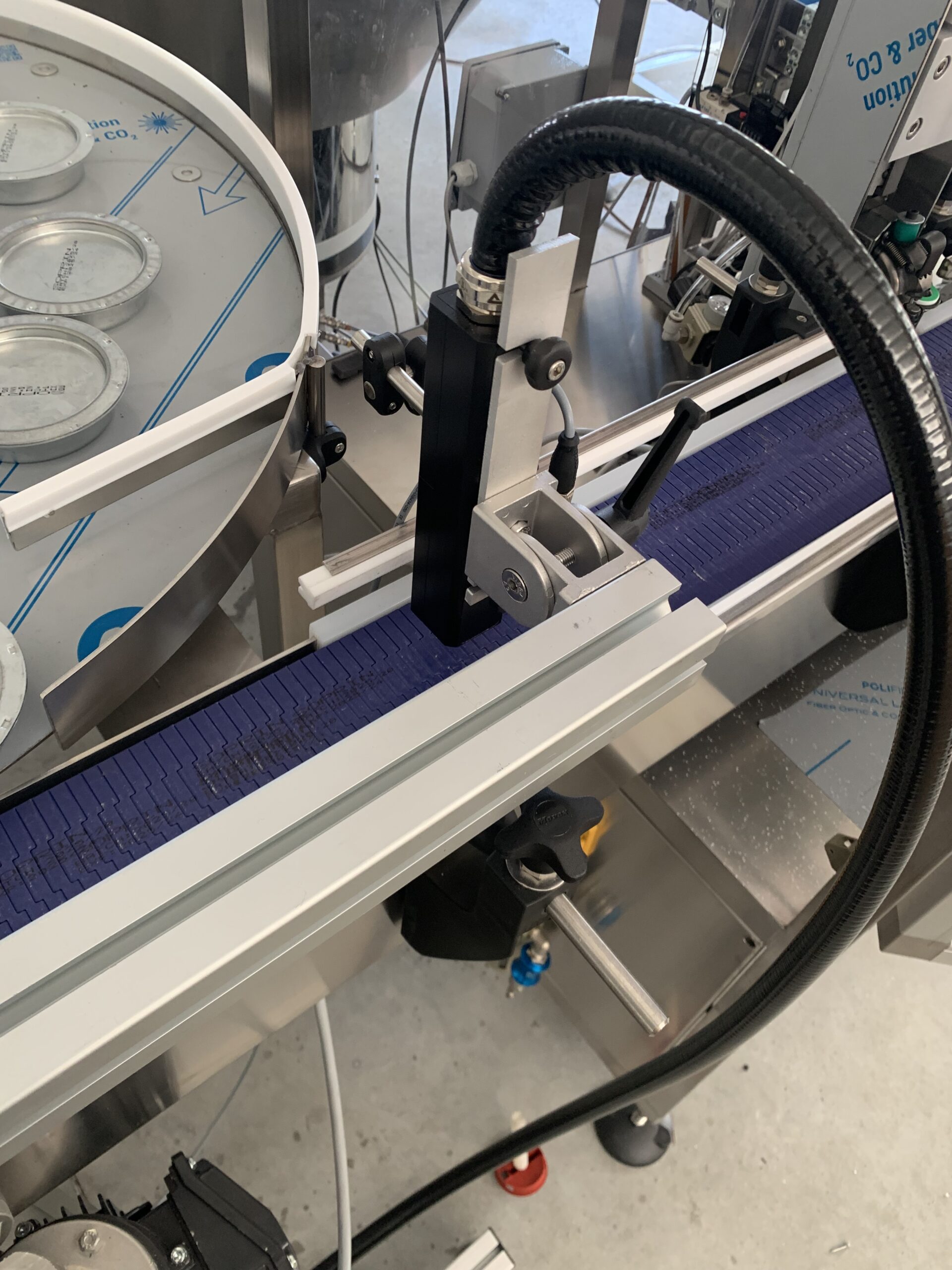
Thermal transfer marker
The project combines CM3 ENGINEERING’s ability to manufacture customised products to specific requirements and is an innovative process project for powder dosing.
The job was realised in about 9 months from the order and allowed the customer to speed up a process that required several manual steps and significant exposure of the operators to the powders to be dosed.