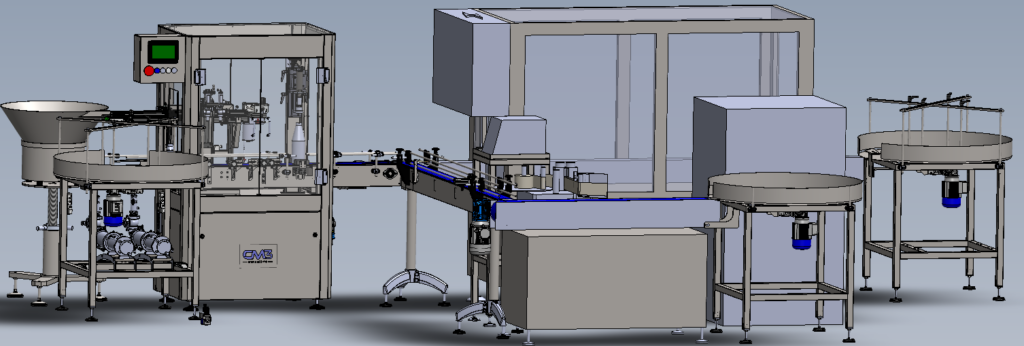
This order involved the creation of a complete fruit juice bottling plant in glass containers with twist off caps in various bottle sizes ranging from 200 ml up to 1,000 ml. The product is taken directly from the customer’s pasteurization plant and dosed at a temperature of approximately 80° with a tailor-made tube circuit.
The entire system was designed by our technical office considering the spaces and dimensions of the customer’s factory and defining a layout that allows optimizing the dimensions and movements of the operators involved in the handling operations of the finished product
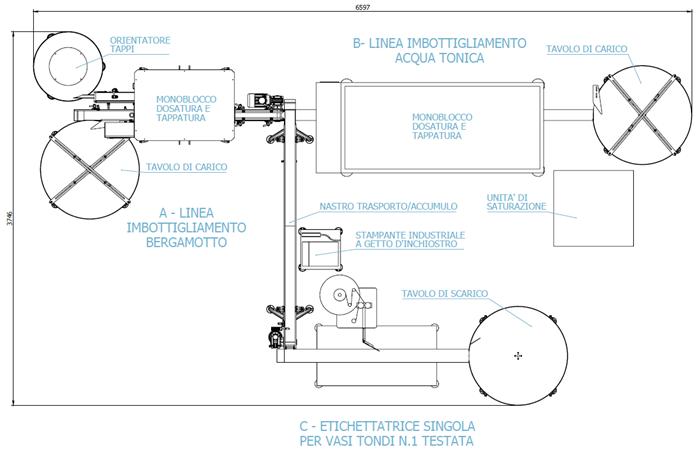
The line consists of an entrance table of Ø 1,000 on which two volumetric dosing pumps have been positioned at the base. The positioning of the latter in this area allows for effective withdrawal of the product from the pasteurization system with a connection that joins the product to be provided in line at the outlet.
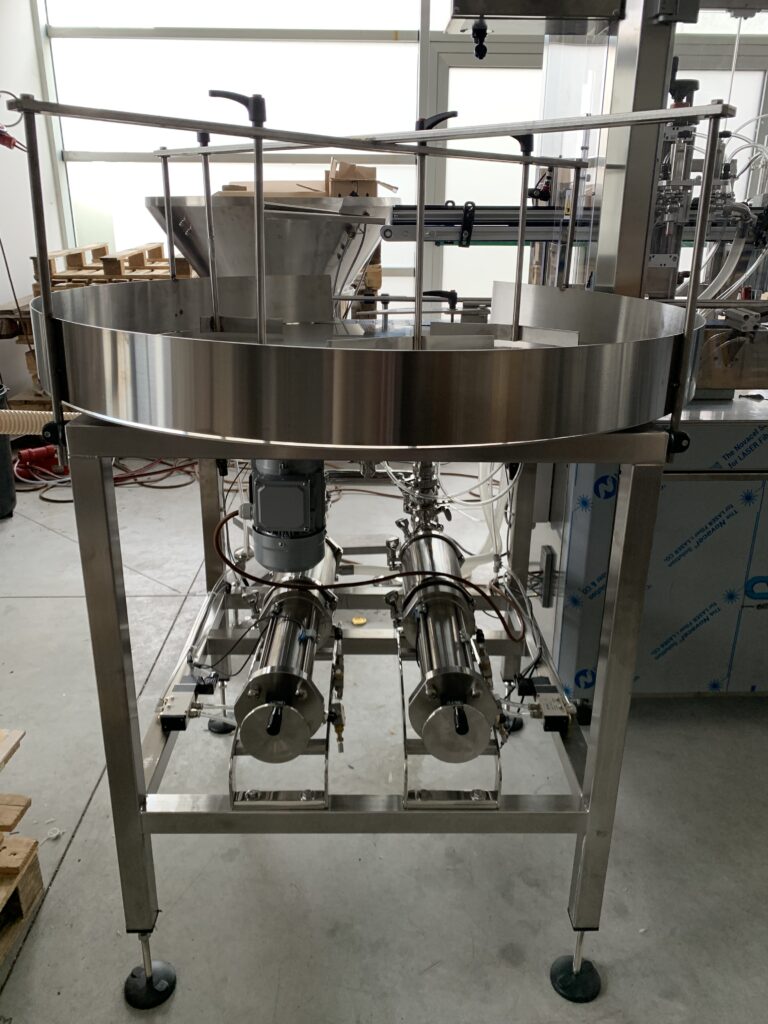
The dosing and capping monoblock includes two nozzles dosing, capping and applying station and head capping machine descending
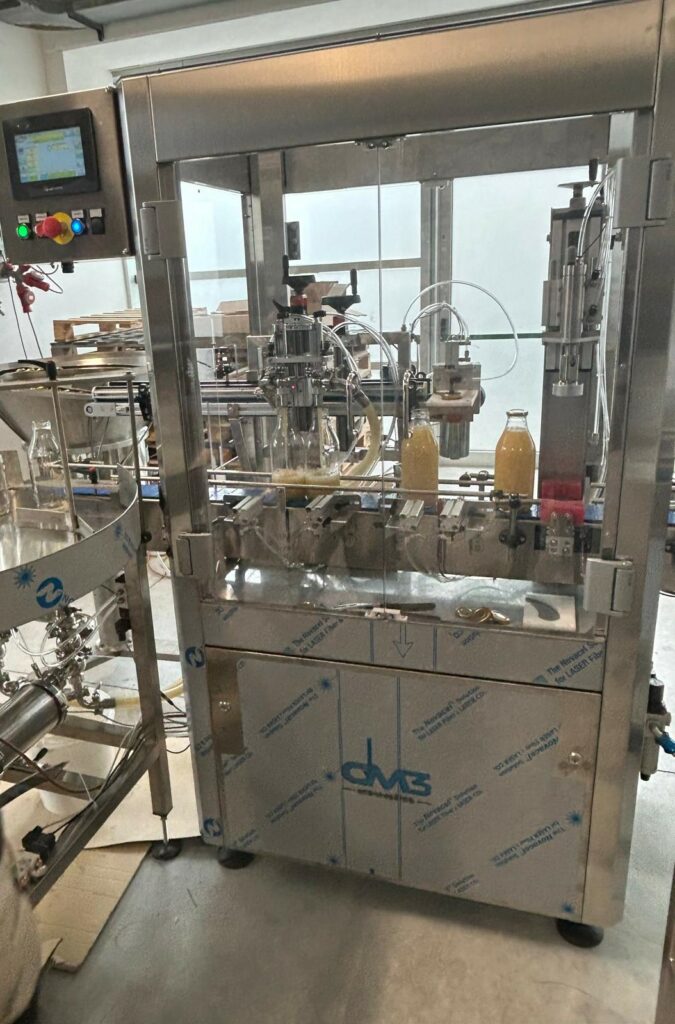
The caps are oriented by a vibration system whose containment tank guarantees a total capacity of approximately 600 pieces (at full load) and is specifically designed to manage the orientation of different cap formats without any format change.
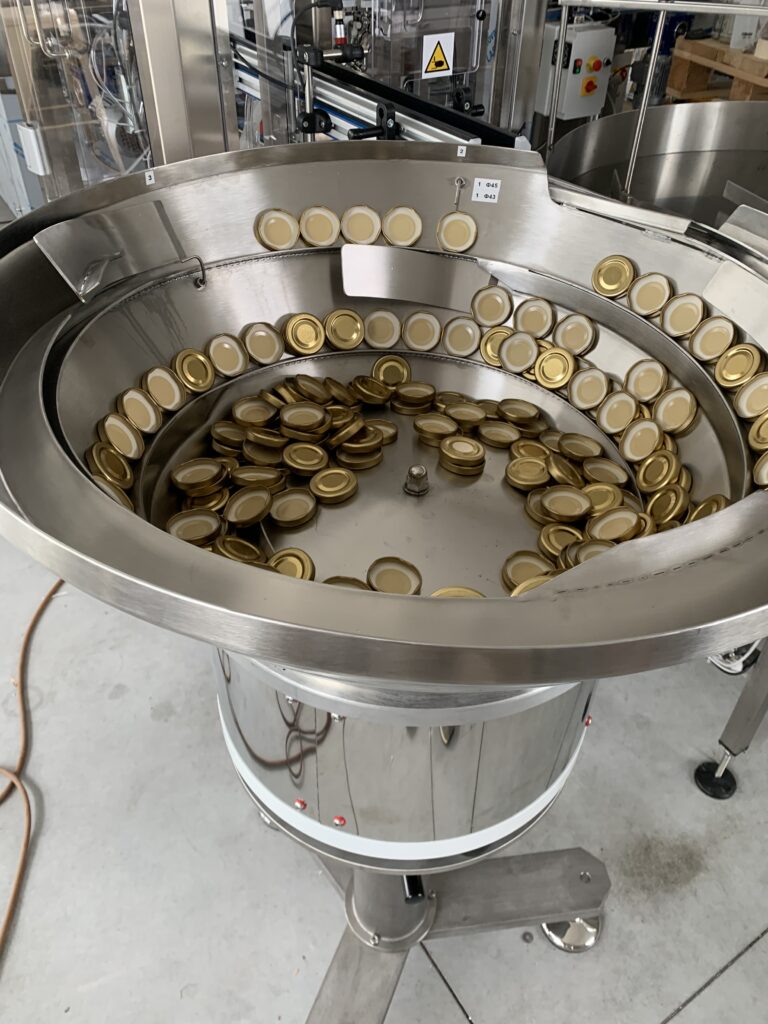
The entire system is made of stainless steel with FDA certified material. Outgoing from the monoblock there is a linear belt of approximately two meters into which the bottles coming out of another isobaric bottling plant also supplied by us are also conveyed. To allow a regular flow of bottles before the labeling process, a manual solution for opening the entrance gate was provided. The single-head labeller completes the packaging process and the finished product is unloaded onto a Ø 1,000 rotary table.
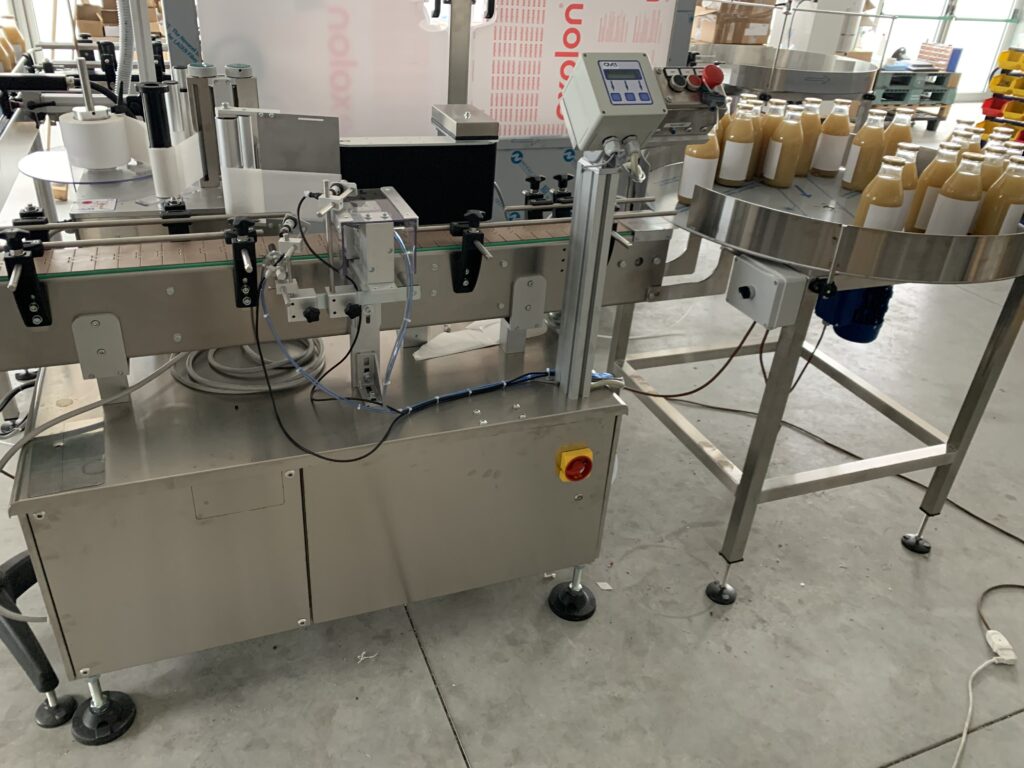