The plant automates the packaging cycle of dense food products that are filled into glass containers of various sizes with twist-off caps.
The main product of this order is truffle cream filled at room temperature in different ranges from 100 g up to 1 kg.
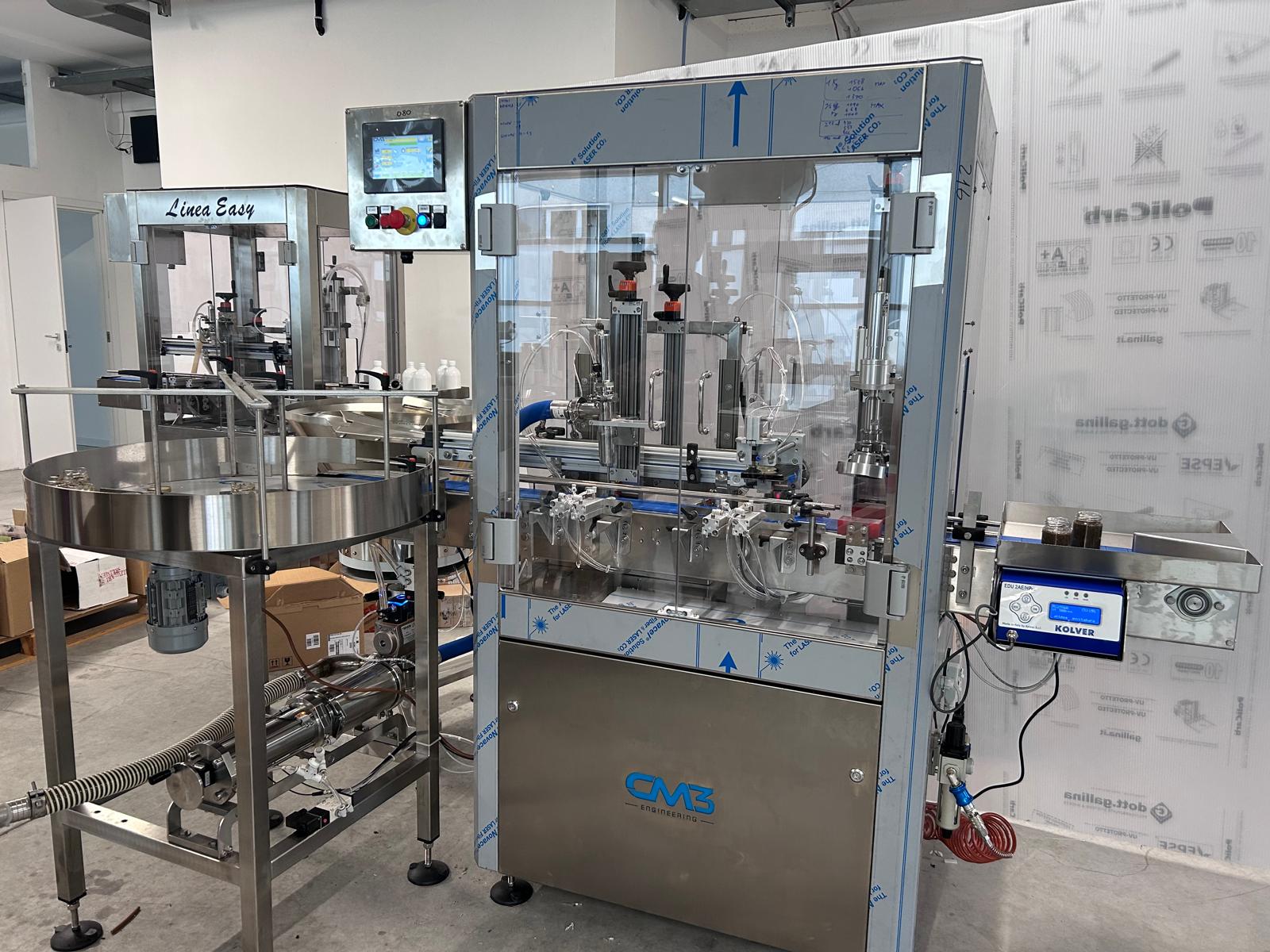
Photo of complete system realised
In a horizontal position with support on the inlet rotary table is positioned the volumetric dispenser prepared with an outlet hole for connection to the product preparation tank in the customer’s possession. The product dispensing spout with Ø 22, inserted inside the monobloc, is specially sized and manufactured to allow the passage of a dense product such as truffle cream with small pieces in suspension.
A descending-head electropneumatic capper with a stainless steel three-gripper chuck has been provided to control the screwing.
The control panel of the capper, integrated in the machine, makes it possible to monitor the twisting of the cork and to signal, in case of criticality, any incorrect closure of the cork by means of an acoustic alarm and a panel signal.
This system guarantees the correct closure of the cork and speeds up the passage to the next pasteurisation cycle.
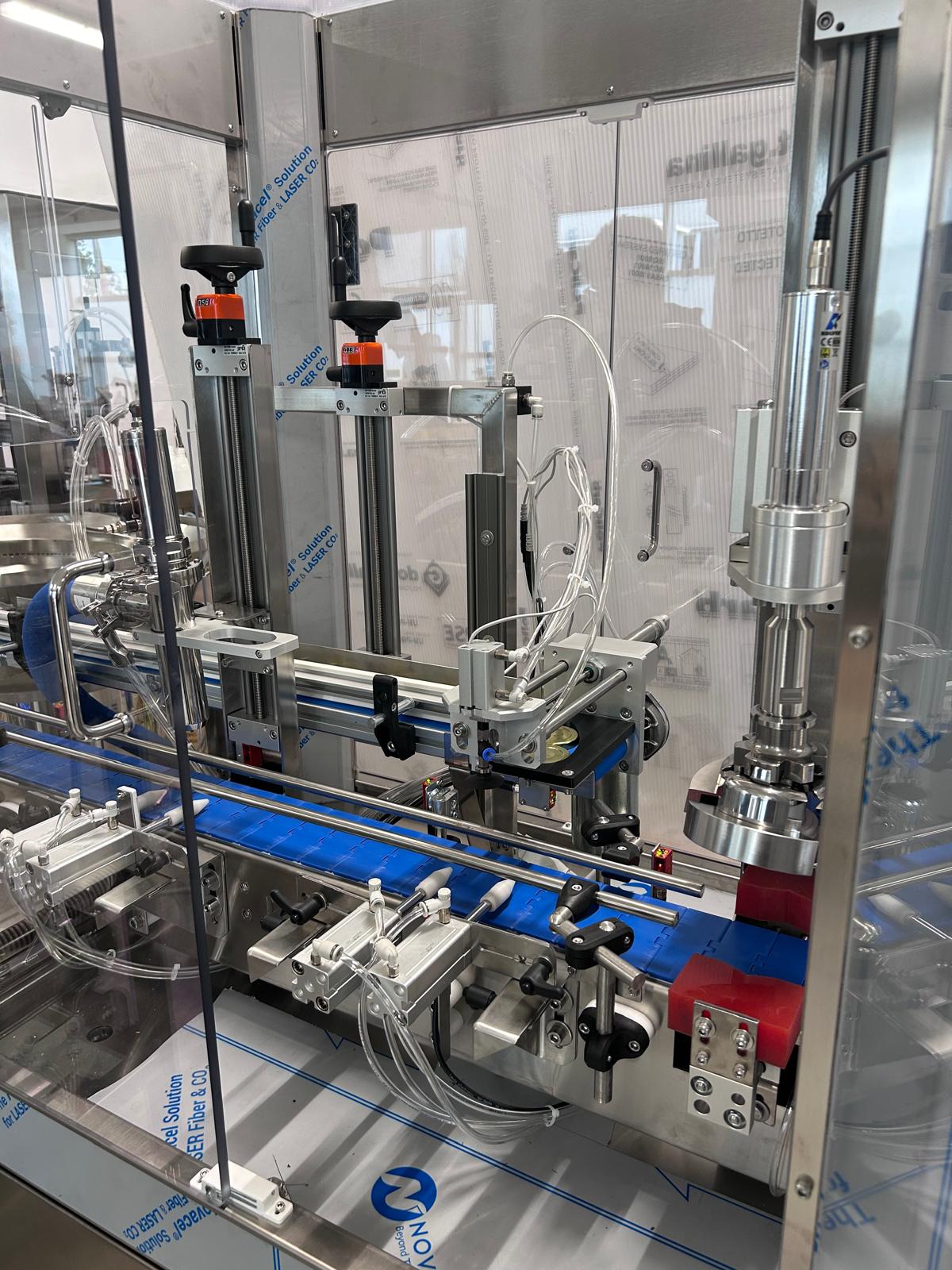
Photo 2 Dispensing spout, pick-and-place station and electropneumatic capper with three grippers
Caps are loaded by means of a vibrating orientator specially designed to handle the three cap formats (Ø 50, Ø 53, Ø 82) with the same tank, a very versatile solution that facilitates time and operations for format changes.
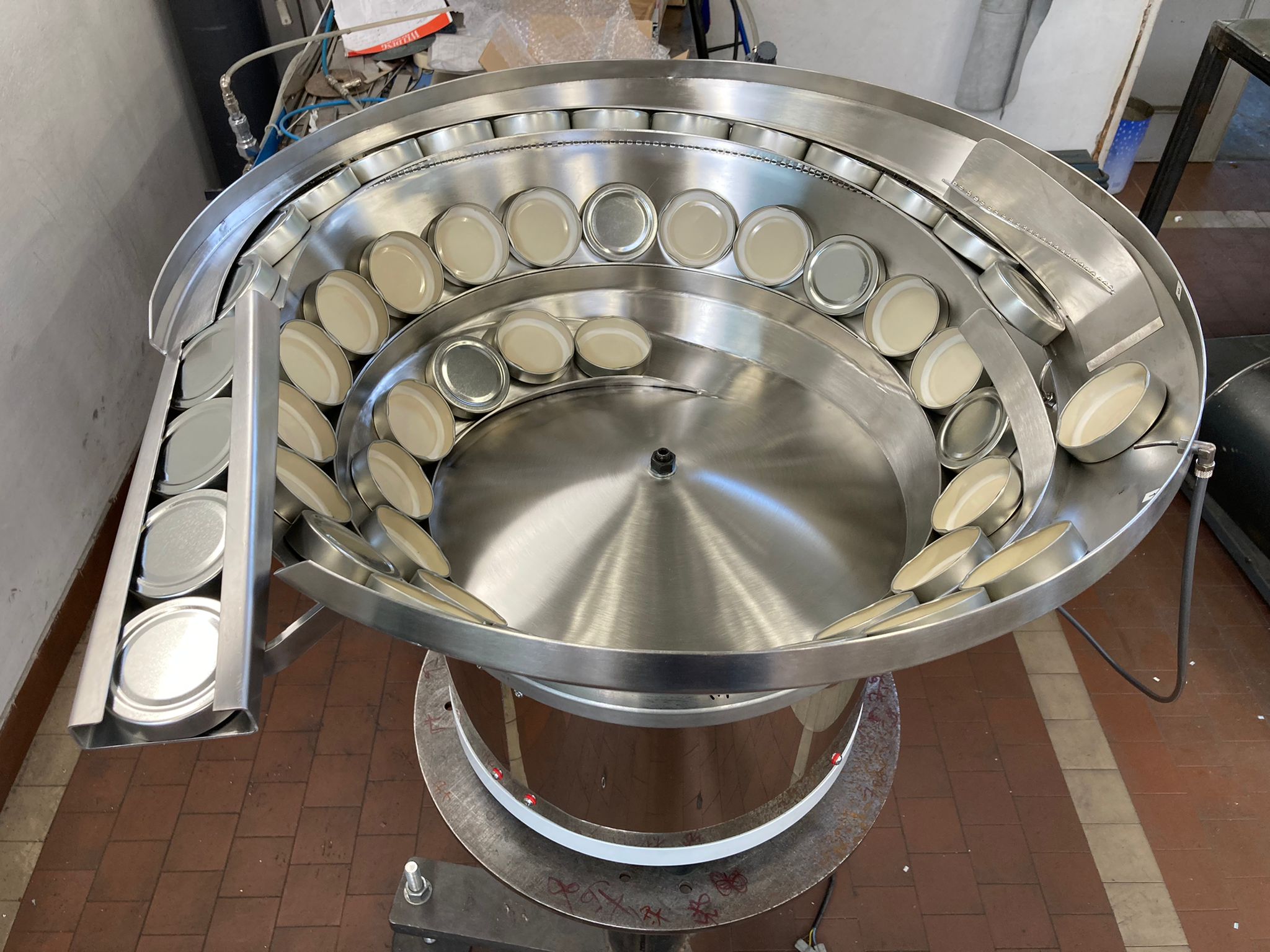
Photo 3 Vibrating orientator for twist-off multiformat caps
The plant achieves a speed of around 900 pieces per hour on the 100 g format and was designed with the possibility of increasing the speed by adding the second dosing unit in the future without having to make any further changes to the structure and control software.
Finally, the project was completed within 4 months of receiving the sample.