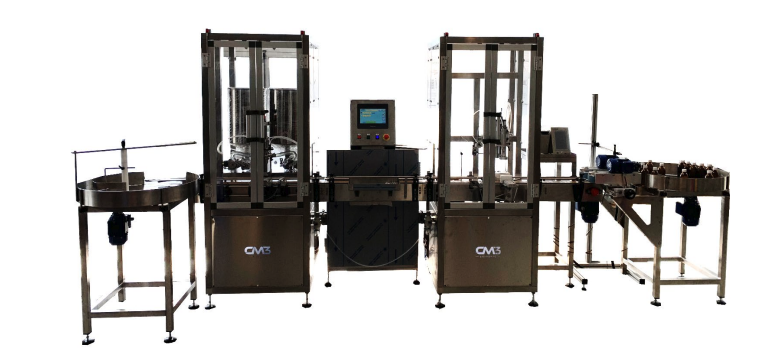
Bei diesem Auftrag unterstützte unser Team den Kunden bei der Gründung eines Kosmetiklabors und schlug ihm von Anfang an die beste Lösung vor, die drei Anforderungen erfüllen sollte:
1) Eine vielseitige Linie, die insgesamt 6 Formate verarbeiten kann, von der kleinsten 20ml-Metallflasche bis zur größten 500ml-Glasflasche mit Schraubverschluss
2) Eine modulare Lösung, die für zukünftige Erweiterungen und Automatisierung ausgelegt ist
3) Eine Lösung, die mit dem verfügbaren Budget vereinbar ist
Bei der Konzeption des Systems wurden die räumlichen Gegebenheiten des neuen Labors des Kunden von Anfang an berücksichtigt, indem die Abmessungen der Anlage an den vorgegebenen Grundriss und den verbleibenden Platz angepasst wurden.
Die Anlage ist, auch im Hinblick auf zukünftige Erweiterungen, mit zwei pneumatisch betriebenen volumetrischen Dosierern mit einem Dosierbereich von 5ml bis 380ml ausgestattet.
Dieser Bereich ermöglicht es, alle Formate in einem einzigen Hub und das größere 500-ml-Format in zwei Hüben zu verarbeiten.
Um eine angemessene Versorgung während der Abfüllphase zu gewährleisten, wurden zwei Trichter mit je 50 Litern Inhalt (einer für jede Zapfanlage) vorgesehen, damit die Anlage die jetzt und in Zukunft erforderlichen Produktionsgeschwindigkeiten gewährleisten kann.
Der Monoblock für das Verschließen hingegen wurde so konzipiert, dass der erforderliche Platz vorhanden ist, um zu einem späteren Zeitpunkt eine mögliche Pick&Place-Station für die automatische Positionierung der Verschlüsse einzubauen – ein Szenario, das es dem Kunden ermöglicht, wenn das Produktionsvolumen dies rechtfertigt, zusätzliche Zeit des Bedienpersonals freizusetzen, die sich auf die Verwaltung des Be- und Entladens des Produkts am Anfang und Ende der Linie beschränkt.
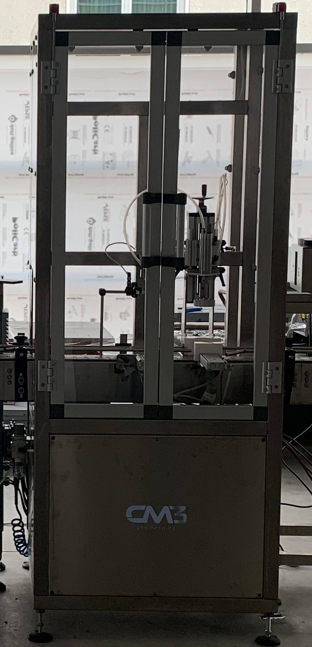
Um diese zukünftige Änderung zu ermöglichen, wurde nicht nur die Verschließeinheit, sondern auch der gesamte elektrische Schaltschrank der Maschine speziell für die notwendigen Automatisierungserweiterungen dimensioniert.
Die Einstellungen für die 6 Formatwechsel sind einfach und leicht zu erlernen und bestehen aus einigen wenigen manuellen Anpassungen der Dosier- und Verschließstationen sowie des Gläsertransportbandes.
Die Maschine kann auch von einem einzigen Bediener bedient werden, der die leeren Gläser auf den Einlaufdrehtisch lädt und sich dann an die Station vor dem Touchscreen-Panel stellt, das spezifische Verarbeitungsrezept lädt und das System startet. Wenn die Maschine läuft, muss der Bediener den Deckel manuell auf das Glas setzen, das am Ende der Linie in den Drehtisch entladen wird.
Die Produktionsgeschwindigkeiten liegen zwischen 1.000 und 1.200 Stück/Stunde (bei einem Maschinenmanagement mit zwei Bedienern) und können mit dem zusätzlichen automatischen Kappenladesystem auf 1.800 Stück/Stunde erhöht werden. (in diesem Fall würde auch die Anwesenheit des zweiten Bedieners entfallen)
Am Ende der Linie, zwischen der Verschließstation und dem sich drehenden Entladetisch, musste ein Tintenstrahlmarkierer die Charge mit dem Verfallsdatum bedrucken, die auf einem kleinen, speziell angefertigten Gestell mit vier Beinen angebracht ist.

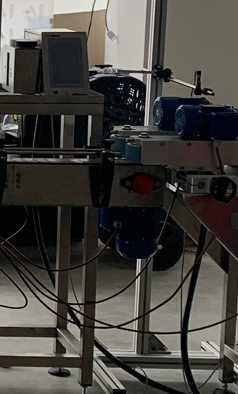
Die Realisierung und Lieferung des Systems dauerte etwa vier Monate ab der Bestellung, und nach einem ersten Test in den Räumlichkeiten von CM3 dauerte die Installation, Inbetriebnahme und Schulung der Mitarbeiter insgesamt vier Tage, gefolgt von Fernsupport-Aktivitäten bei Bedarf des Kunden mit der Aktivierung eines Servicevertrags.
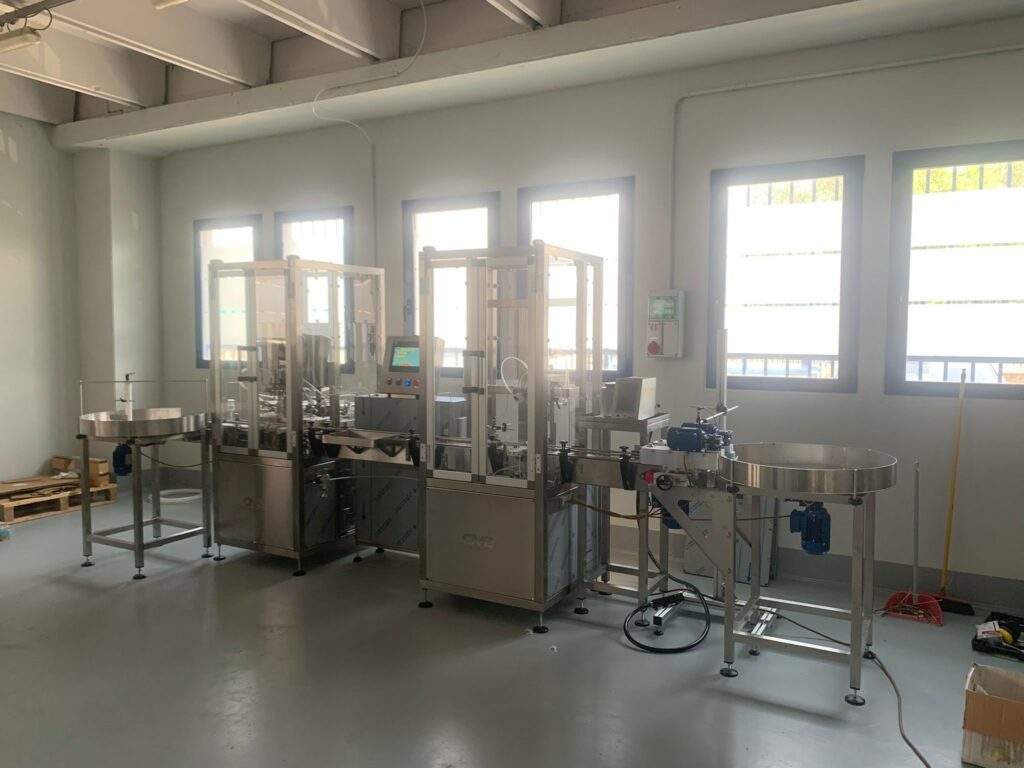
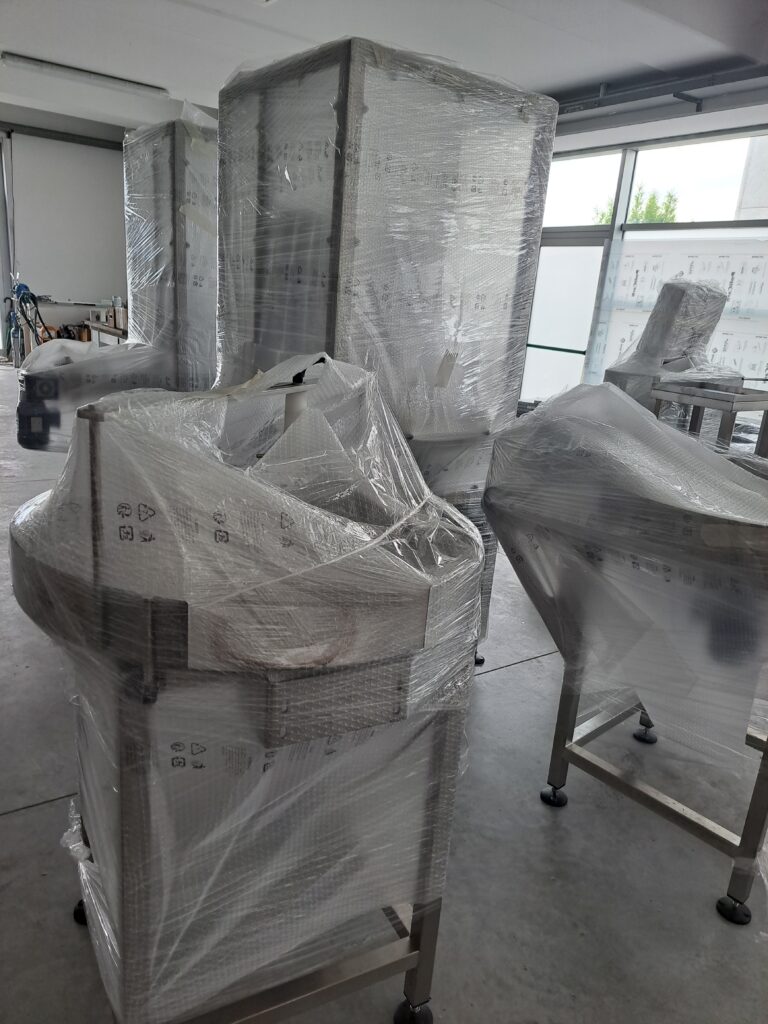
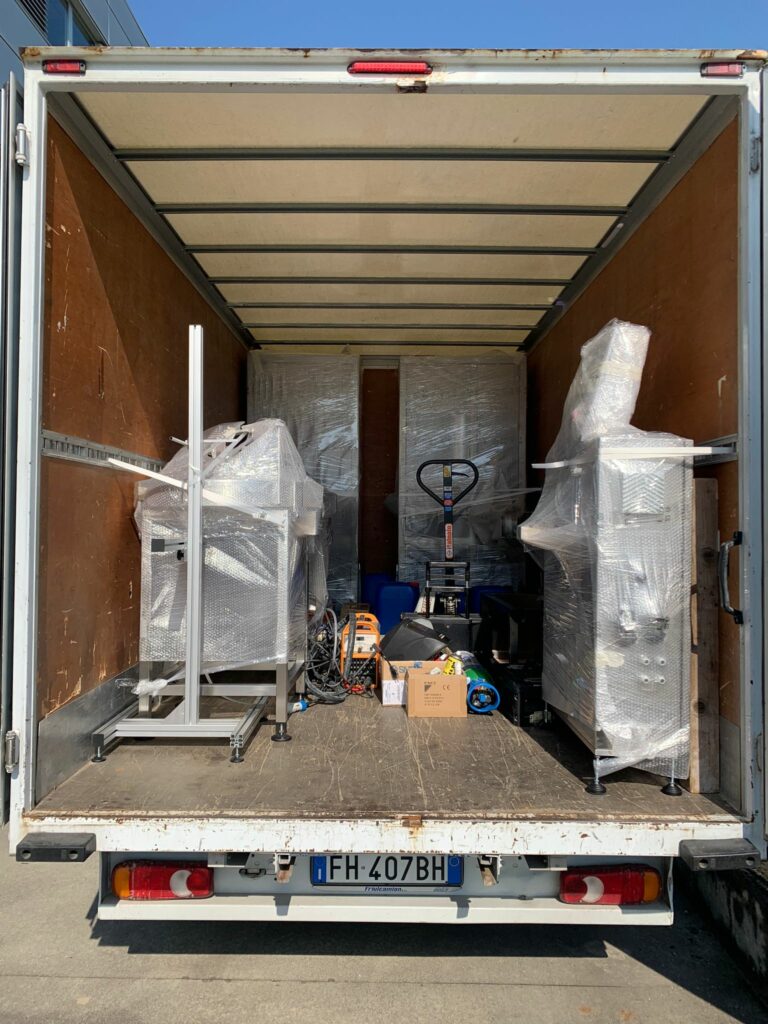