Dieser Auftrag umfasste die Studie und die maßgeschneiderte Realisierung einer automatischen Linie, die für den Verpackungsprozess von Pulverprodukten in einem zylindrischen Metallbehälter geeignet ist, auf den nach der Füllphase des Produkts das Silikon aufgetragen und der Deckel durch einen Clinch-Prozess verschlossen wird.
Um das Layout der Anlage zu definieren, das auf dem Foto unten zu sehen ist, war unser Ingenieurteam etwa drei Monate lang mit der Untersuchung, Feinabstimmung und Auswahl der geeigneten Materialien für die Handhabung der Pulver und der verschiedenen Stationen des gesamten Verpackungsprozesses beschäftigt.
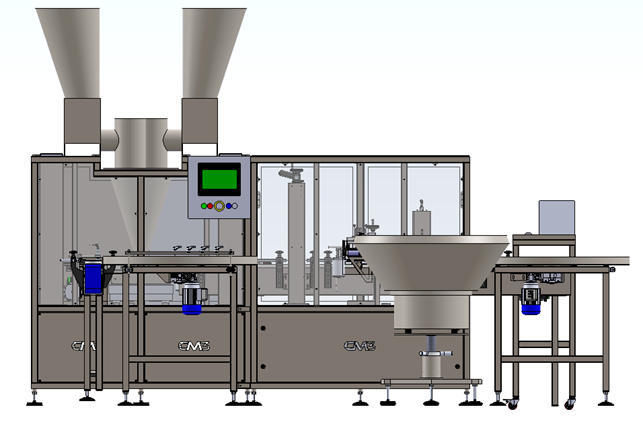
Vollständiges Anlagenlayout in 3D
Ein Drehtisch mit einem Durchmesser von 1.000 mm wurde bereitgestellt, um die leeren Kartons etwa stündlich in die Verpackungslinie einführen zu können.
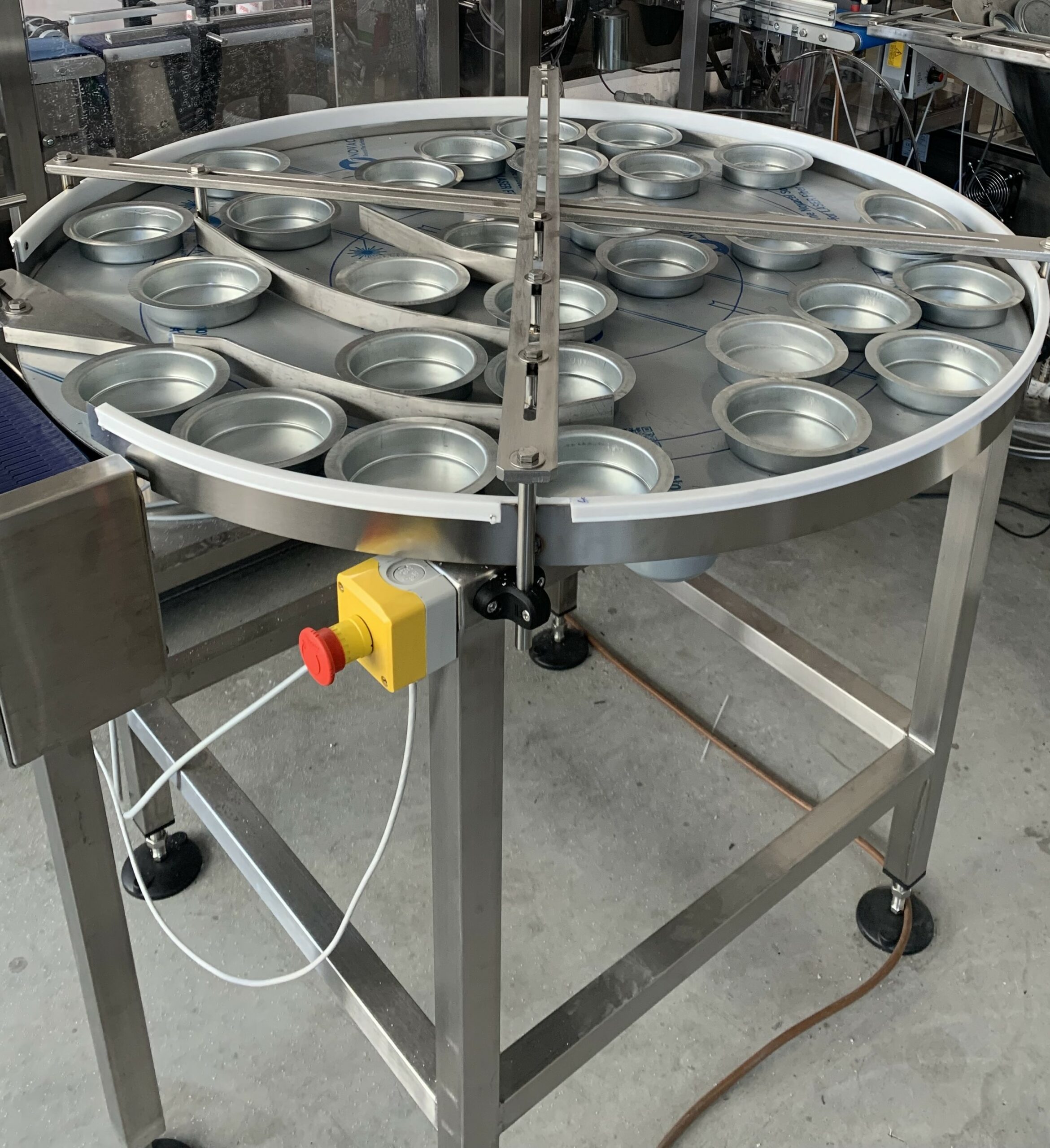
Foto rotierender Containerladetisch am Anfang der Linie
Am Eingang des Monoblocks befindet sich die Dosierstation, die aus zwei separaten Schneckendosierern mit Ladetrichtern besteht, die speziell aus rostfreiem Stahl gefertigt und mit expandiertem Hastelloy C-276 PTFE ausgekleidet sind und in die zwei verschiedene Produkte geladen werden.
Das Produkt wird in einen konischen Trichter befördert, der das Produkt in den Behälter fallen lässt, der auf einer speziellen Wägezelle ruht, die das richtige Gewicht überwacht. Der Standard-Dosiervorgang erfolgt in drei automatischen Schritten: PRODUKT A (Gewicht) – PRODUKT B (Gewicht) und PRODUKT A (Gewicht). Die verschiedenen Verarbeitungsrezepte, Einzelgewichte und Produktraten können über das Touchscreen-Panel eingestellt werden.
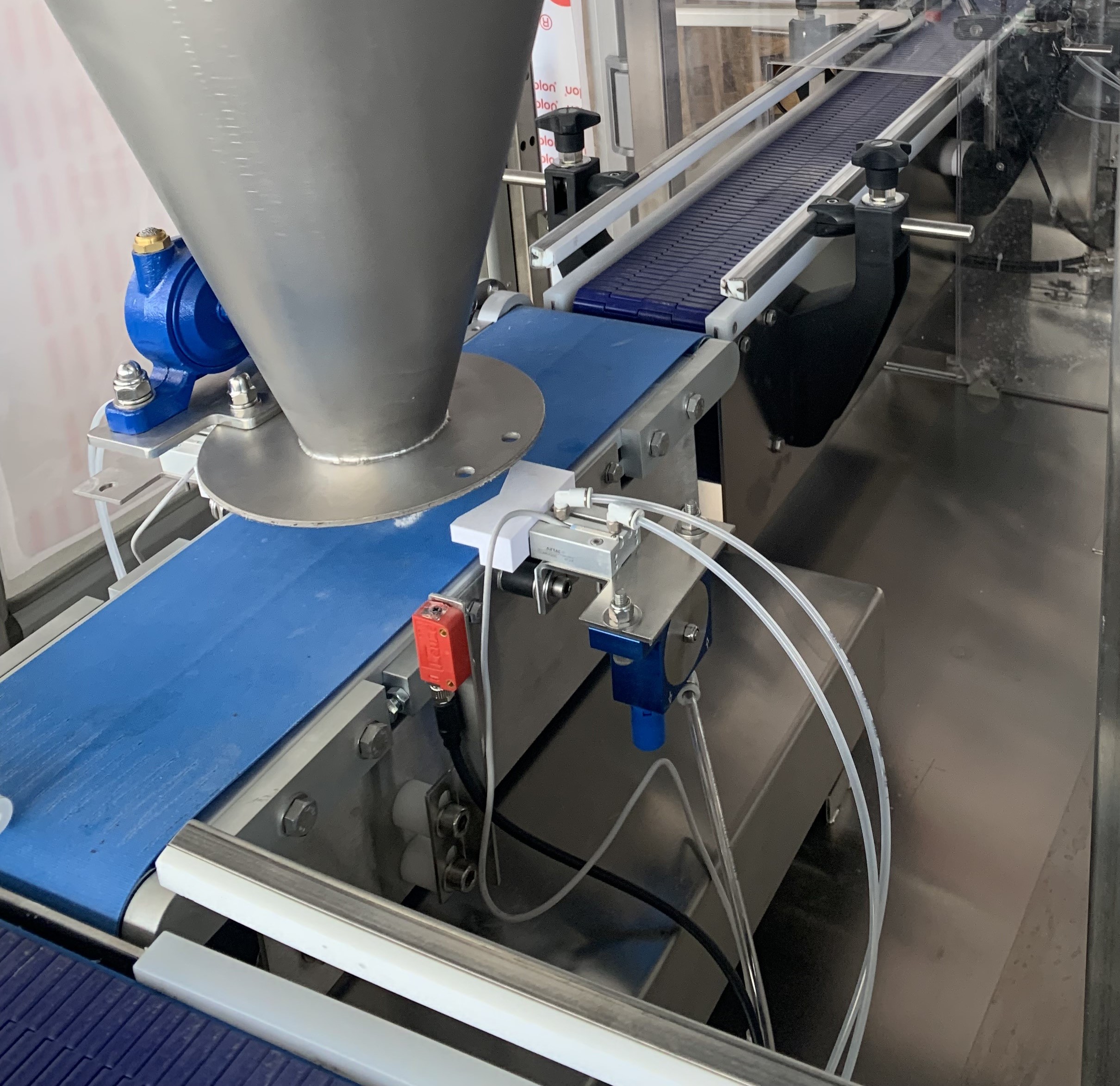
Bild Dosierstation auf Wägezelle
Im weiteren Verlauf des Verarbeitungszyklus befindet sich die Silikonisierungsstation, in der der Behälter mit Hilfe von Drehmodulen gedreht wird, damit das Silikon um den gesamten Rand herum aufgetragen werden kann.
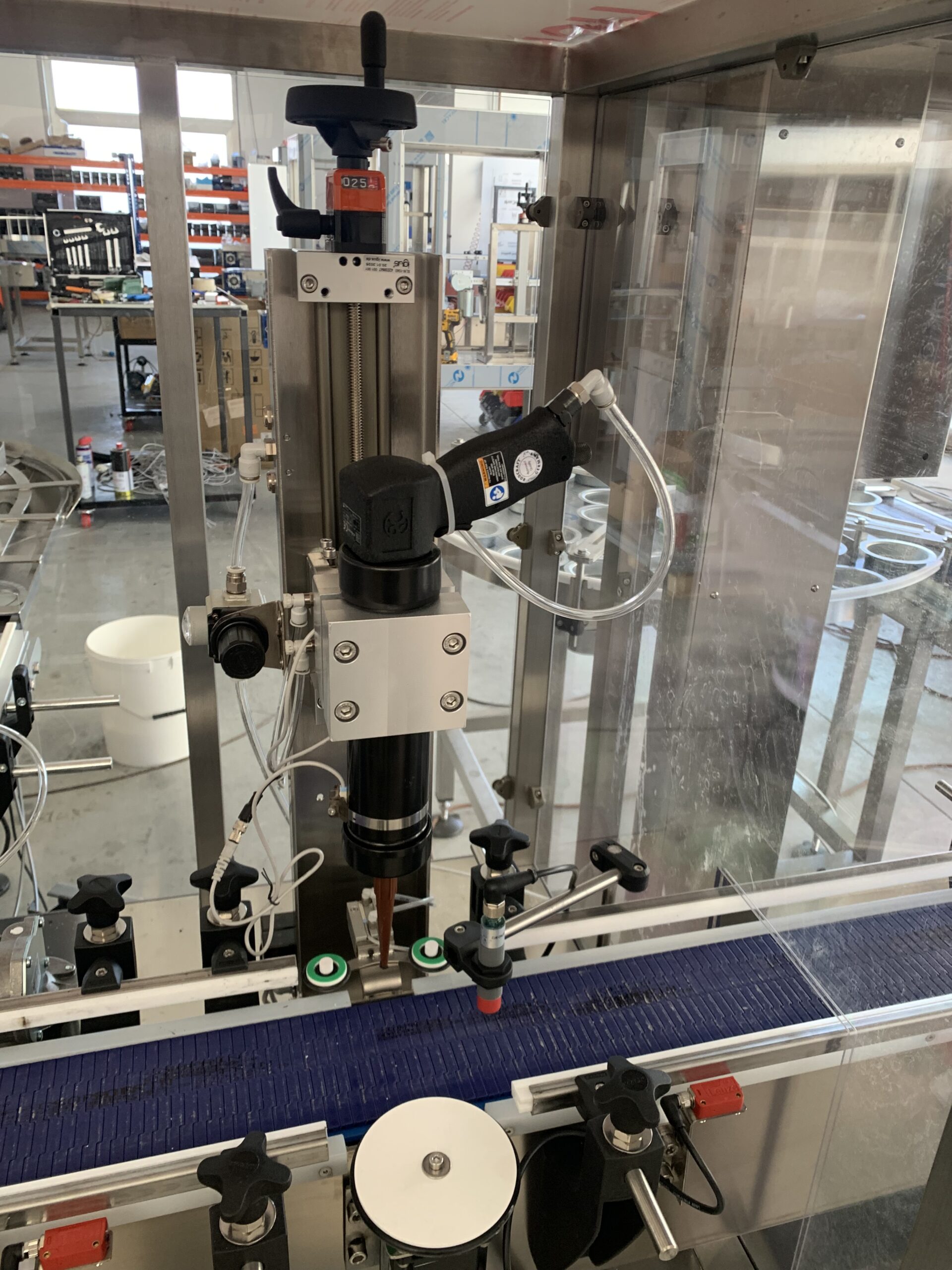
Siliconisierungsstation mit Rotationssystem
Als nächstes nimmt der Pick-and-Place-Picker die Deckel auf, die durch einen vibrierenden Orientierer automatisch auf das Spezialband geladen werden, und legt sie auf den Behälter, wobei er sanften Druck ausübt, damit das Silikon schnell aushärten kann.
Der letzte Verpackungsschritt, das Clinchen, erfolgt nach dem gleichen Rotationsprinzip, indem der Deckel an 7 verschiedenen Punkten auf den Behälter gestanzt wird.
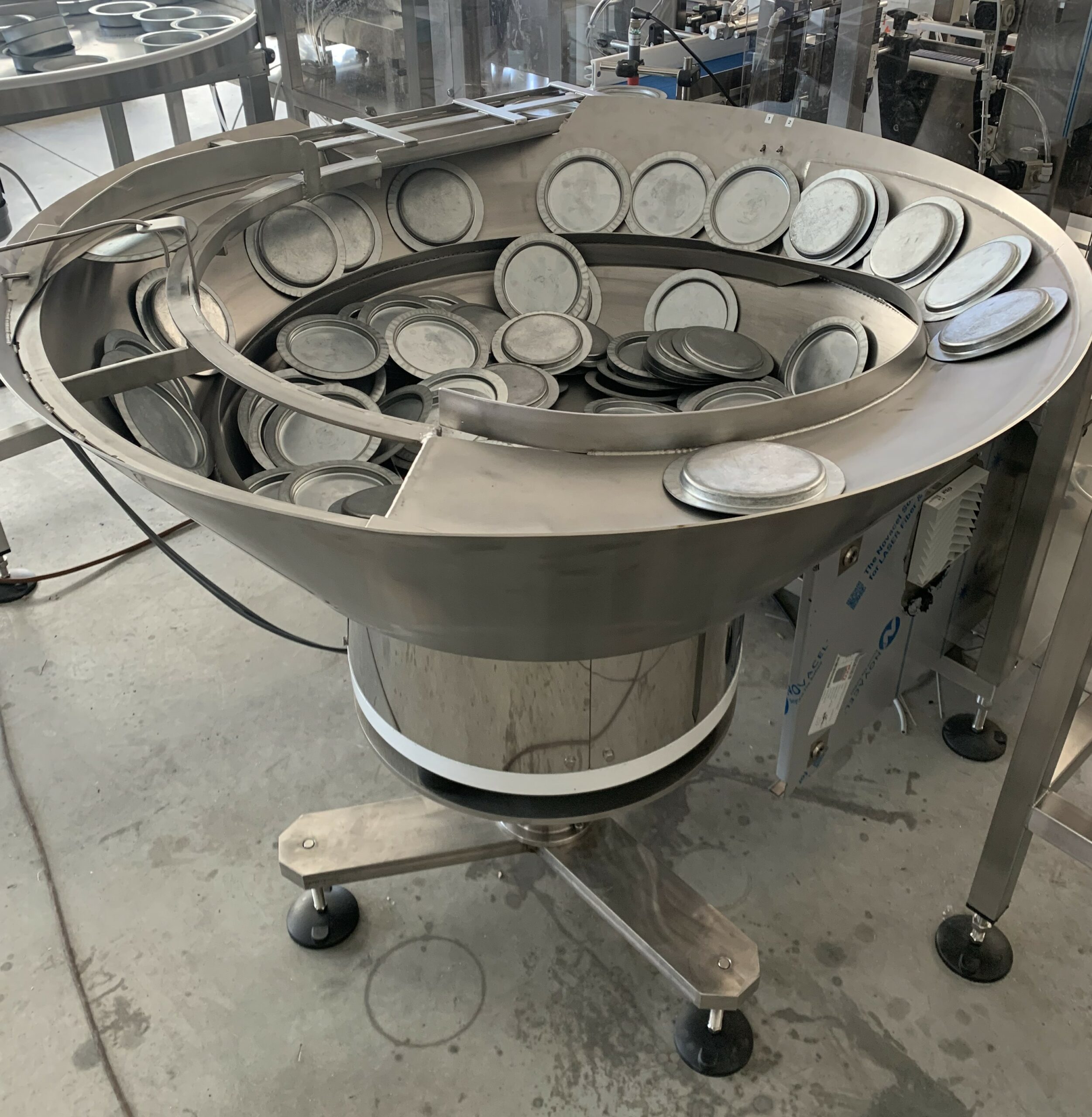
Bild Vibrierende Metalldeckel-Orientierungshilfe
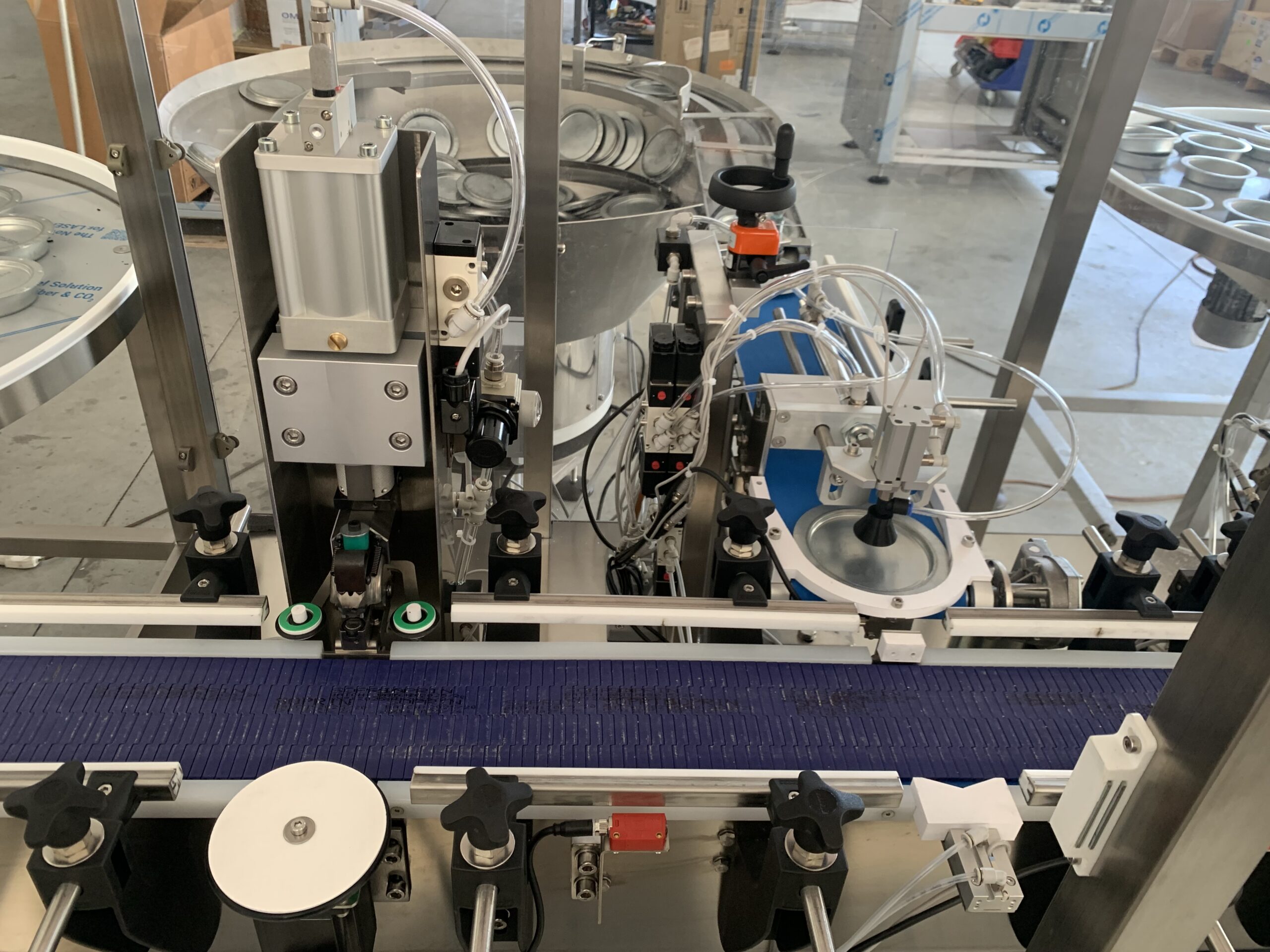
Bild PICK&PLACE Pick-and-Place-Station
Am Ausgang des Monoblocks befindet sich ein Thermotransferdrucker für die Kennzeichnung der Produktionscharge und des Produkts sowie ein Drehtisch mit einem Hub von 1.000 mm.
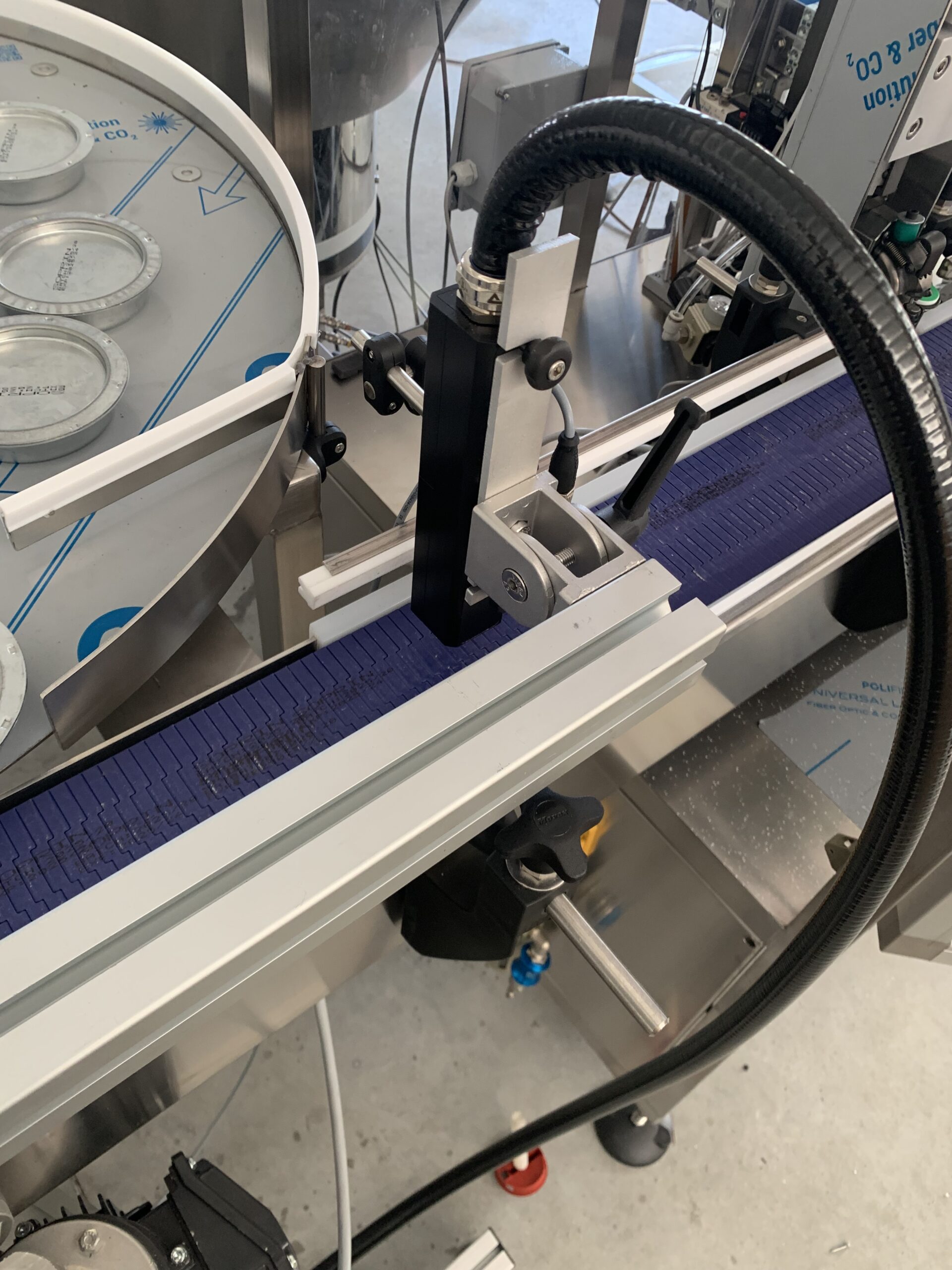
Thermotransfer-Marker
Das Projekt vereint die Fähigkeit von CM3 ENGINEERING, maßgeschneiderte Produkte für spezifische Anforderungen herzustellen, und ist ein innovatives Prozessprojekt für die Pulverdosierung.
Der Auftrag wurde in etwa 9 Monaten ab Bestellung realisiert und ermöglichte es dem Kunden, einen Prozess zu beschleunigen, der mehrere manuelle Schritte und eine erhebliche Exposition des Bedienpersonals gegenüber den zu dosierenden Pulvern erforderte.