This commission involved the creation of a complete system for filling chlorine-based (anti-mold) products in PET bottles from 250 ml to 750 ml with the application of a child-safe plastic cap.
In a first phase, we studied the product as it was really corrosive, after that, we decided to equip the system with a vertical dosing group with a PMMA cylinder and a HDPE head piston for the dosing part. Then we decided to protect the internal frame of the monobloc, with a very resistant powder coating.
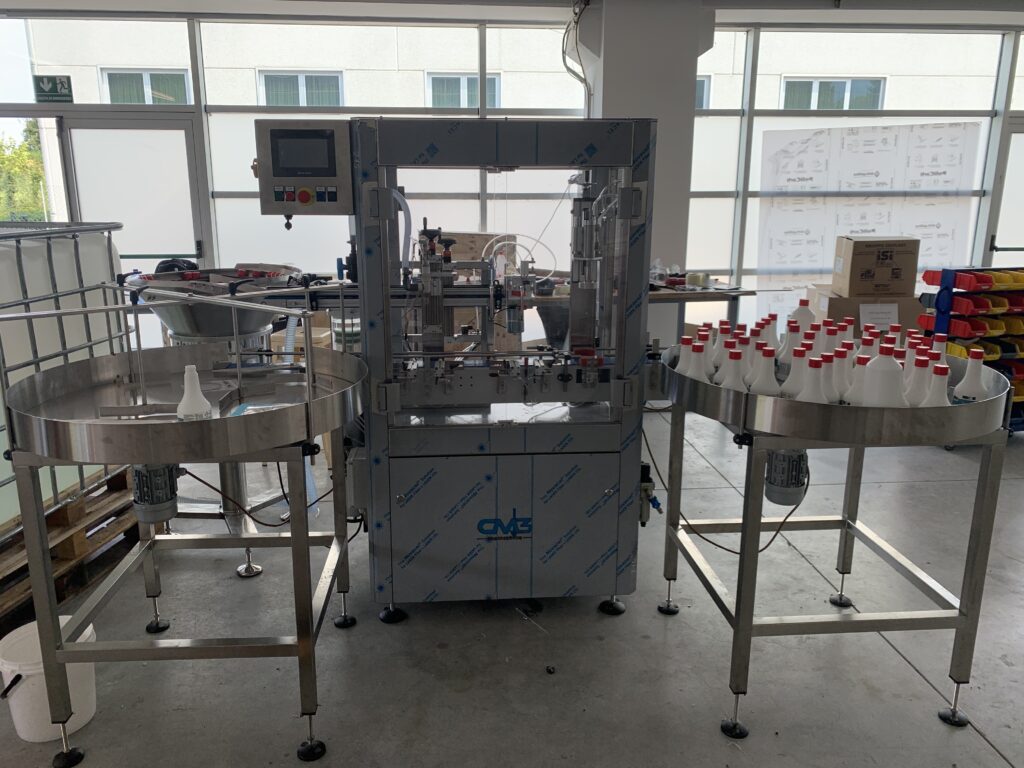
Picture of the line
Stainless steel rotary tables Ø 1,000, located at the beginning and at the end of the line, allow the system to be managed by a single operator who has just to take care of the loading and unloading of the containers.
The customer need was to have the possibility to handle 3 different cap formats with one orientor, that is what our orientor can perfectly do. It is positioned behind the loading rotary table and has a capacity of approximately 900 caps. The operator will have to fill it approximately every hour.
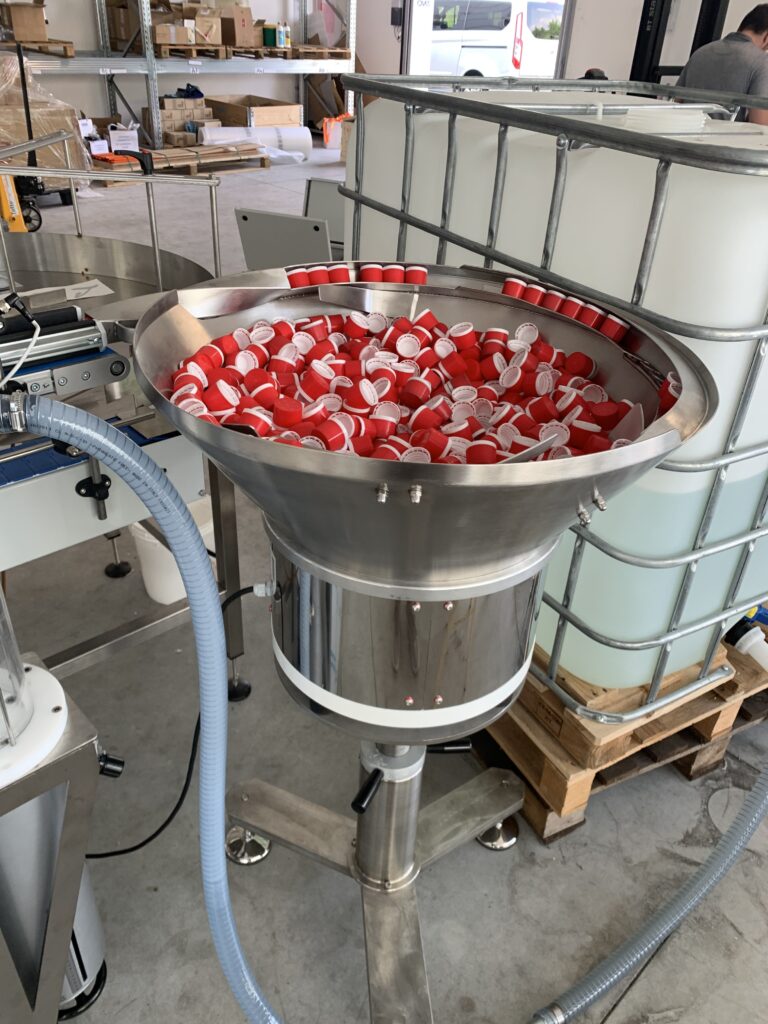
PIC.1: Vibrating cap orientor for placstic caps
The line is completed by a 7″ touch screen panel, placed in front of the operator, with integrated software for storing processing recipes and managing the automation of the entire line.
The line overall has a encumbrance of approximately 2.5 linear meters and a height of 1,8 mt.
It has beed delivered to the customer approximately in 4 months from the order receipt.